Schott casts first main mirror segments for ESO's Extremely Large Telescope (WITH VIDEO)
The first six hexagonal segments for the main mirror of the European Southern Observatory's (ESO's) Extremely Large Telescope (ELT) have been successfully cast by Schott (Mainz, Germany) at their facility in Mainz. These segments will form parts of the ELT's 39 m main mirror, which will have 798 segments in total when completed. The ELT will be the largest optical telescope in the world when it sees first light in 2024.
RELATED ARTICLE: Schott and Safran Reosc awarded 39 m mirror contract for ESO's Extremely Large Telescope
The 39 m diameter primary mirror of ESO's ELT will be by far the largest ever made for an optical-infrared telescope. Such a giant is much too large to be made from a single piece of glass, so it will consist of 798 individual hexagonal segments, each measuring 1.4 m across and about 5 cm thick. The segments will work together as a single huge mirror to collect tens of millions of times as much light as the human eye. SEE VIDEO:
As with the telescope's secondary mirror blank, the ELT main mirror segments are made from the low-expansion ceramic material from Schott. ESO has awarded this German company with contracts to manufacture the blanks of the first four ELT mirrors (known as M1 to M4, with M1 being the primary mirror).
The first segment castings are important as they allow the engineers at Schott to validate and optimize the manufacturing process and the associated tools and procedures.
The casting of the first six segments is a major milestone, but the road ahead is long--in total more than 900 segments will need to be cast and polished (798 for the main mirror itself, plus a spare set of 133). When fully up to speed, the production rate will be about one segment per day.
After casting, the mirror segment blanks will go through a slow cooling and heat treatment sequence and will then be ground to the right shape and polished to a precision of 15 nm across the entire optical surface. The shaping and polishing will be performed by Safran Reosc (Saint Pierre du Perray, France), which will also be responsible for additional testing.
SOURCE: ESO; http://www.eso.org/public/news/eso1801/
About the Author
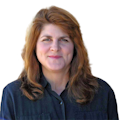
Gail Overton
Senior Editor (2004-2020)
Gail has more than 30 years of engineering, marketing, product management, and editorial experience in the photonics and optical communications industry. Before joining the staff at Laser Focus World in 2004, she held many product management and product marketing roles in the fiber-optics industry, most notably at Hughes (El Segundo, CA), GTE Labs (Waltham, MA), Corning (Corning, NY), Photon Kinetics (Beaverton, OR), and Newport Corporation (Irvine, CA). During her marketing career, Gail published articles in WDM Solutions and Sensors magazine and traveled internationally to conduct product and sales training. Gail received her BS degree in physics, with an emphasis in optics, from San Diego State University in San Diego, CA in May 1986.