Double-sided molded plastic optics have two microstructured surfaces
Suhl, Germany--CDA GmbH, which manufactures molded microstructured plastic optical and microfluidic devices, says that it now can manufacture double-sided molded structures. The company does this through wafer-level production and molds optimized for precise double-sided alignment.
CDA can mold microstructured optics from various plastics, including polycarbonate, PMMA and cyclo-olefin-copolymers) and can integrate multiple elements into a single device. The multiple structures can form any combination of refractive microoptical elements and arrays, diffractive structures (DOEs) and optical diffusors for optics, and microfluidic structures and surface structuring for analytical lab-on-a-chip applications.
Applications of microstructured optics include holographic optics, laser beam-shaping diffusers (see figure), LED beam-shaping diffusers, refractive/diffractive lenses, and others.
Bonded multielement devices are possible
The upper and lower molds of the structure are manufactured separately and are then positioned to tolerances of +/-5 µm or less for the molding process. Multiple double-sided structures with differing functionalities can be layered (stacked) to the same positional accuracy and subsequently permanently bonded. The bonding process ensures full compatibility with adverse environments, and in particular with sensitive biological systems, says CDA.
CDA notes that uses include structured illumination in optics, microscopy, miniaturized analytical instrumentation, and so on; other optoelectronics; clinical point-of-care and other diagnostics tasks; and environmental monitoring and biochemical/forensic screening applications.
For more info, see: http://www.cda-microworld.com
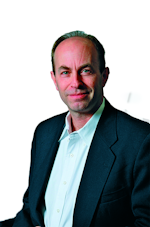
John Wallace | Senior Technical Editor (1998-2022)
John Wallace was with Laser Focus World for nearly 25 years, retiring in late June 2022. He obtained a bachelor's degree in mechanical engineering and physics at Rutgers University and a master's in optical engineering at the University of Rochester. Before becoming an editor, John worked as an engineer at RCA, Exxon, Eastman Kodak, and GCA Corporation.