Biologically inspired piezo actuator lets robotic camera mimic human eye movement
Atlanta, GA--Georgia Institute of Technology (Georgia Tech) researchers are using piezoelectric materials to replicate the muscle motion of the human eye to control camera systems in a way designed to improve the operation of robots. This new, biologically inspired (biomimetic) muscle-like action could help make robotic tools safer and more effective for MRI-guided surgery and robotic rehabilitation.
The new control system is based on a piezoelectric cellular actuator that allows a robot eye to move more like a real eye. The research is being conducted by Ph.D. candidate Joshua Schultz under the direction of assistant professor Jun Ueda, both from the George W. Woodruff School of Mechanical Engineering at Georgia Tech.
"For a robot to be truly bio-inspired, it should possess actuation, or motion generators, with properties in common with the musculature of biological organisms," said Schultz. "The actuators developed in our lab embody many properties in common with biological muscle, especially a cellular structure. Essentially, in the human eye muscles are controlled by neural impulses. Eventually, the actuators we are developing will be used to capture the kinematics and performance of the human eye."
Details of the research were presented June 25, 2012, at the IEEE International Conference on Biomedical Robotics and Biomechatronics in Rome, Italy. The research is funded by National Science Foundation. Schultz also receives partial support from the Achievement Rewards for College Scientists (ARCS) Foundation.
Ueda, who leads the Georgia Tech Bio-Robotics and Human Modeling Laboratory in the School of Mechanical Engineering, said this novel technology will lay the groundwork for investigating research questions in systems that possess a large number of active units operating together. The application ranges from industrial robots, medical and rehabilitation robots to intelligent assistive robots.
"Robustness against uncertainty of model and environment is crucial for robots physically interacting with humans and environments," said Ueda. "Successful integration relies on the coordinated design of control, structure, actuators and sensors by considering the dynamic interaction among them."
The cellular actuator concept developed by the research team was inspired by biological muscle structure that connects many small actuator units in series or in parallel. The high-speed approach includes a single-degree of freedom camera positioner that can be used to illustrate and understand the performance and control of biologically inspired actuator technology. This new technology uses less energy than traditional camera positioning mechanisms and is compliant for more flexibility.
"Each muscle-like actuator has a piezoelectric material and a nested hierarchical set of strain amplifying mechanisms," said Ueda. "We are presenting a mathematical concept that can be used to predict the performance as well as select the required geometry of nested structures. We use the design of the camera positioning mechanism’s actuators to demonstrate the concepts."
In the study, the scientists sought to resolve a previous conundrum. A cable-driven eye could produce the eye's kinematics, but rigid servomotors would not allow researchers to test the hypothesis for the neurological basis for eye motion. "Each muscle-like actuator consists of a piezoelectric material and a nested hierarchical set of strain amplifying mechanisms," said Ueda. "Unlike traditional actuators, piezoelectric cellular actuators are governed by the working principles of muscles--namely, motion results by discretely activating, or recruiting, sets of active fibers, called motor units. Motor units are linked by flexible tissue, which serves a two-fold function," said Ueda. "It combines the action potential of each motor unit, and presents a compliant interface with the world, which is critical in unstructured environments."
The Georgia Tech team has presented a camera positioner driven by a novel cellular actuator technology, using a contractile ceramic to generate motion. The team used 16 amplified piezoelectric stacks per side. The use of multiple stacks addressed the need for more layers of amplification. The units were placed inside a rhomboidal mechanism. The work offers an analysis of the force-displacement tradeoffs involved in the actuator design and shows how to find geometry that meets the requirement of the camera positioner, said Schultz.
"The goal of scaling up piezoelectric ceramic stacks holds great potential to more accurately replicate human eye motion than previous actuators," noted Schultz. "Future work in this area will involve implantation of this technology on a multi-degree of freedom device, applying open and closed loop control algorithms for positioning and analysis of co-contraction phenomena."
SOURCE: Georgia Institute of Technology; http://gtresearchnews.gatech.edu/muscle-like-action-mimics-human-eye-movement/
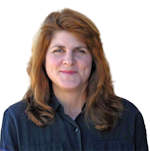
Gail Overton | Senior Editor (2004-2020)
Gail has more than 30 years of engineering, marketing, product management, and editorial experience in the photonics and optical communications industry. Before joining the staff at Laser Focus World in 2004, she held many product management and product marketing roles in the fiber-optics industry, most notably at Hughes (El Segundo, CA), GTE Labs (Waltham, MA), Corning (Corning, NY), Photon Kinetics (Beaverton, OR), and Newport Corporation (Irvine, CA). During her marketing career, Gail published articles in WDM Solutions and Sensors magazine and traveled internationally to conduct product and sales training. Gail received her BS degree in physics, with an emphasis in optics, from San Diego State University in San Diego, CA in May 1986.