Laser inspection helps trains stay on track
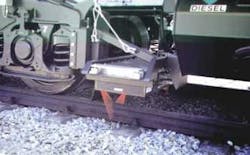
Everyday passengers of intercity and commuter railways may not be aware that lasers are keeping them safe and on schedule. The Optical Rail Inspection and Analysis (ORIAN) system made by KLD Labs (Huntington Station, NY) is a practical application of optoelectronics that uses a laser, video camera, and data-analysis software to create a real-time report on rail conditions (see figure).
Mounted underneath the truck of a railroad vehicle traveling at up to 185 mph, the ORIAN system measures the cross-sectional profile and dimensions of both rails from the base to the top of the rail surface to an accuracy of 0.005 in. Such accuracy is required to ensure an optimal wheel-to-rail interface. The shape of the rail is critical to minimize the interaction between vehicle and track. "Rails deform over time, and can wear to extreme limits before they need replacement," says Daniel Magnus, vice president of KLD. However, the rail can be reprofiled and optimized with the assistance of rail-grinding machines.
The ORIAN inspection systems are installed on some of the fastest passenger trains in the United States and Europe, reporting the overall condition of the track in real time. "Some of our systems process over 40 Mbytes of data per second," says Magnus. "In milliseconds we have an answer about the condition of the track. This blows away typical machine-vision rates in manufacturing."
One type of system uses four near-infrared diode lasers to illuminate the left and right side of each rail. A high-resolution video camera then records an image of the rails using charge-coupled devices. Next, image-processing software provides a real-time user interface that allows railroad personnel to immediately identify sections of track that require attention.
One of the challenges in rail inspection is filtering out sunlight, which creates intense blooming on the raw data. "Throughout the northern regions in the world where the Sun is on the horizon for days, the top of the rail is almost like a mirror," says Magnus. To remedy the problem, the system uses a combination of high-intensity lasers and a filter design that minimizes the effect of the solar spectrum on the image.
Other challenges include precise alignment and calibration for the two cameras. Also, the housing must isolate the system from shock and vibration of up to 80 Gs and be able to resist rain, snow, dust, and grease. The systems have been modified and developed since their first appearance in 1986 at the World Exposition in Vancouver, Canada, and are now deployed in 75 systems in 22 countries.
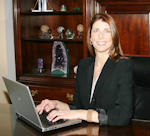
Valerie Coffey-Rosich | Contributing Editor
Valerie Coffey-Rosich is a freelance science and technology writer and editor and a contributing editor for Laser Focus World; she previously served as an Associate Technical Editor (2000-2003) and a Senior Technical Editor (2007-2008) for Laser Focus World.
Valerie holds a BS in physics from the University of Nevada, Reno, and an MA in astronomy from Boston University. She specializes in editing and writing about optics, photonics, astronomy, and physics in academic, reference, and business-to-business publications. In addition to Laser Focus World, her work has appeared online and in print for clients such as the American Institute of Physics, American Heritage Dictionary, BioPhotonics, Encyclopedia Britannica, EuroPhotonics, the Optical Society of America, Photonics Focus, Photonics Spectra, Sky & Telescope, and many others. She is based in Palm Springs, California.