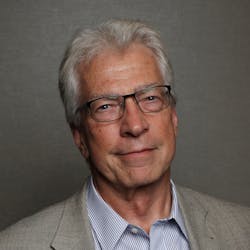
The business and environmental costs are high for using fungicides and insecticides on agricultural crops. For example, maleic hydrazide and Prime Plus kill the sucker or auxillary buds on green tobacco plants; however, these chemicals can leave high residue levels on the cured leaf or in the soil. Beginning in 1993, R.C. Long of the crop-science department at North Carolina State University (Raleigh, NC) began exploring ways to use alternative suckercides such as C6 to C12 fatty alcohols that are contact-based and do not leave undesirable residues.
Traditionally, suckercides are applied as a banded spray over the top of plant rows. To be effective, the fatty alcohol suckercides must collect and run down the stalk, making contact with the sucker buds that grow at the junction of each leaf with the stalk. Applying these suckercides directly to the broad leaves can sometimes burn holes in the leaves, thereby reducing cured leaf quality and market value.
Manually applying the fatty alcohols directly over the top of the stalk is highly effective in killing the suckers and eliminating leaf burn. Yet labor costs have made this method impractical. Therefore, Long and his team set out to find a way to automatically determine the location of the stalk of each plant and applying a minimal amount of suckercide as a pulsed spray directly over the stalk.
Top notch
The first application of a suckercide is often combined with topping—removing the flower from the top of the plant to allow the remaining leaves to mature before harvest—and topping is usually performed by a cutting head pulled by a tractor. Therefore, Long developed a system that performed both operations.
Inside the cutting and spraying compartment, a near-IR through-the-beam sensor mounted immediately below the topper blade locates the plant stalks and tracks the plants passing under the topper head until they reach a spray head and the suckercide can be applied as a short burst. The system deployed in 2006 to locate the position of the stalk used a smart-camera color machine-vision system that provides better than 95% accuracy for the suckercide application.
Long’s design needed the vision system to identify the stalk location of each plant, track the plant as it moved through the topper, and trigger a spray pulse to apply just enough suckercide to do the job—about 15 ml, compared to approximately 30 ml per plant for traditional applications. This all needs to be accomplished in the field at speeds of 2.5 mph and higher, where the 22 in. spacing of the plants translates to roughly two plants topped and sprayed per second. To refine the system, Long called in Jeff and Carolyn Fleming at Industrial Automation Consultants (Charlotte, NC), a vision-system integrator.
Behind the curtain
The team developed a system that uses Velcro-removable black-cloth side curtains on the compartment containing the topper and sprayer to eliminate both direct and ambient light. A Cognex (Natick, MA) 552C color CCD smart camera running Intellect image-processing software is focused down on the rows as plants pass through the topper and guide belts. “We were trying to keep all the processing in the camera for speed and power considerations,” explains Fleming. “Things happen rather quickly when you are rolling through the field.” The camera comes with a built-in six-LED white-light source, but the team developed a high-brightness LED illuminator capable of strobing.
Although the system was developed for use with tobacco, Long believes the discrimination power and processing speed of the system lend themselves to a wide range of uses, such as application of fungicides, insecticides, herbicides, and foliar nutrients in a variety of other agricultural, vegetable, and nursery crops.
“This technology,” asserts Long, “holds the potential of many benefits for both the environment and agricultural production.” His list of benefits includes directing the application of agrochemicals to the site of desired activity, increasing efficacy of the application, reducing the volume of chemical used, reducing production costs, reducing or eliminating undesirable residues, reducing chemical drift and worker exposure, and reducing the potential for soil and groundwater contamination.
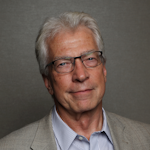
Conard Holton
Conard Holton has 25 years of science and technology editing and writing experience. He was formerly a staff member and consultant for government agencies such as the New York State Energy Research and Development Authority and the International Atomic Energy Agency, and engineering companies such as Bechtel. He joined Laser Focus World in 1997 as senior editor, becoming editor in chief of WDM Solutions, which he founded in 1999. In 2003 he joined Vision Systems Design as editor in chief, while continuing as contributing editor at Laser Focus World. Conard became editor in chief of Laser Focus World in August 2011, a role in which he served through August 2018. He then served as Editor at Large for Laser Focus World and Co-Chair of the Lasers & Photonics Marketplace Seminar from August 2018 through January 2022. He received his B.A. from the University of Pennsylvania, with additional studies at the Colorado School of Mines and Medill School of Journalism at Northwestern University.