Aerotech software-based PLC integrates with motion controller
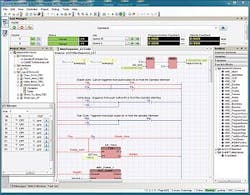
The A3200 MotionPAC software-based programmable logic controller (PLC) integrates with the company's A3200 motion controller, or can be used independently for full machine control or in conjunction with AeroBasic programs. Programming in Ladder Diagrams (LD), Function Block Diagrams (FBD), or Structured Text (ST) is possible. Integration with the A3200 motion controller allows users to command asynchronous, coordinated, blended, geared, or cammed motion directly from LD, FBD, or ST, or directly start or stop AeroBasic programs.
Aerotech
Pittsburgh, PA
[email protected]
-----
PRESS RELEASE
A3200 MotionPAC – Integrated PLC and Advanced Motion Controller Provides 30% to 50% Reduction in Development Time
PLC totally integrated with advanced motion
Standards based: IEC 61131-3, PLCopen and .NET
30% to 50% reduction in development time
Global Tag database – define Tags once and use everywhere
Easy to use diagnostics and debugging tools
Aerotech’s A3200 MotionPAC is a software-based Programmable Logic Controller (PLC) that is completely integrated with Aerotech’s A3200 motion controller to increase programming efficiency, decrease development time and to increase quality. The MotionPAC can be used independently for full machine control or in conjunction with AeroBasic™ programs, and complies with IEC 61131-3 and PLCopen. Users can program in Ladder Diagrams (LD), Function Block Diagrams (FBD) or Structured Text (ST). The MotionPAC's Integrated Automation will reduce programming and commissioning time by 30% to 50% and is ideal for machine control program development.
The MotionPAC's tight integration with the A3200 motion controller allows users to command asynchronous, coordinated, blended, geared or cammed motion directly from LD, FBD, ST or directly start or stop AeroBasic™ programs. Moves can be specified as relative or absolute in user units (either English or metric). Additionally, CNC or G code also can be called from the PLC program.
Programmers can create shared variables and Tags that are referenced by Name in all of the A3200 tools, Operator Interface, AeroBasic™, C or .NET programs. Memory management is automatically handled by the MotionPAC for all Tags and variables. Of course, the programmer is free to view the memory addresses or even assign addresses if desired, but it is not necessary.
MotionPAC tools such as user definable libraries (LD, FBD, ST or .NET), integrated axis manager for readout and manual control, global Tag database, automatic memory management and virtual execution of the PLC increase your programming efficiency and quality. Both .NET and PLC programmers can seamlessly collaborate through MotionPAC to deploy machine control applications since the .NET programs can be packaged as an LD, FBD or ST that run in the real-time CLR. Standard fieldbuses, drive I/O and high-end data acquisition are integrated into the MotionPAC and can be shared among all applications by Name. Toolboxes are provided for each language for drag and drop programming or just start typing on the palette and the editor will assist in the programming. The programming palette is free-form meaning that function blocks and functions can be used on a ladder diagram rung as well, even motion function blocks, making programming easy. All of the usual hardware associations, task assignments and programs are organized in an easy-to-use tree structure.
For further information, please contact Steve McLane at 412-967-6854 (direct), or via e-mail at [email protected].
The MotionPAC series data sheet is available at: http://www.aerotech.com/products/pdf/MotionPAC.pdf
-----
Follow us on Twitter
Subscribe now to Laser Focus World magazine; it's free!