Miniature integrating-sphere light source easily calibrates microscopes
Radiometric (intensity) calibration for fluorescence microscopes allows results from two different microscopes to be directly compared if both are properly calibrated (especially important for microscopes “home-built” by the researcher). While fluorescent beads can be used for this purpose, a self-luminous standard radiance source such as an LED makes calibration simpler. Researchers at the National Institute of Metrology (Beijing, China) have developed for this purpose a miniaturized LED-based integrating-sphere light source (LED-ISLS) that includes, in a monolithic structure, an LED, electronics, a battery, and a 4-mm-diameter integrating sphere; the assembly forms a rugged solid polymer module easily mounted and transported.
Experimental devices were constructed containing LEDs with center wavelengths of 468, 519, 595, and 644 nm, respectively, and full widths at half maximum (FWHMs) of 22.9, 26.2, 13.3, and 15.1, respectively. The relative spectral power density distributions of each of the devices was accurately characterized (a requirement for calculation of the spectrally integrated radiance of each LED-ISLS). The temporal stability of each device was characterized at four power levels: 25%, 50%, 75%, and 100% of the maximum level of DC forward current; temporal stability was generally best at the highest power level and fell in the range of about 0.3% to 0.5%. The nonuniformity of radiant exitance at the integrating-sphere exit aperture was also measured and was found to be approximately 0.8%. The radiance of the LED-ISLS devices ranged from 5 W m−2 sr−1 to 69 W m−2 sr−1 and the combined standard uncertainty was 1.3%. The devices allow calibration of the radiance responsivity of fluorescence and other microscopes to within an uncertainty of 2.9% or less. Reference: Y. Fu et al., Opt. Express (2020); https://doi.org/10.1364/oe.403899.
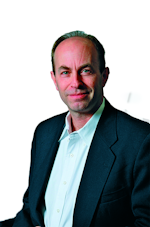
John Wallace | Senior Technical Editor (1998-2022)
John Wallace was with Laser Focus World for nearly 25 years, retiring in late June 2022. He obtained a bachelor's degree in mechanical engineering and physics at Rutgers University and a master's in optical engineering at the University of Rochester. Before becoming an editor, John worked as an engineer at RCA, Exxon, Eastman Kodak, and GCA Corporation.