While it’s still early in the game, LiDAR remains a focal point as automotive manufacturers prepare to meet the anticipated demand for SAE Level 4 autonomy. The likelihood LiDAR will at least be in the mix is high. As a result, what is expected to be a $2.23 billion market in 2022 is estimated to reach $4.71 billion by 2030, representing a conservative CAGR of 9.8%. According to Grand View Research’s report, various performance-based concerns including the “increasing demand for 3D imagery, increasing deployment of automotive safety technology, and growing environmental concerns” serve as key drivers.
Fortunately, LiDAR technology and component manufacturers continue to make great strides in addressing performance concerns including a track record of providing reliable driver assistance and constantly improving environmental sensing capabilities. And, the reality is, the technology behind today’s LiDAR solutions is still maturing.
However, when putting all the components together to achieve autonomy, a few potentially significant obstacles still exist, such as the need to miniaturize technology to fit within existing automotive model constraints. While the thirst for autonomy continues to grow, neither automakers nor consumers want the technology to significantly alter the aesthetics of a vehicle.
Why have we continued to dig into the various aspects of LiDAR? Simply put, those intimately familiar with the applicable photonics components are paying close attention. According to a recent survey of our readership, LiDAR is not just a significant area of interest for our engineering heavy audience, respondents also identify the technology as one of the most important for the future success of their companies.
The common technology for automotive LiDAR application is the pulse or time of flight (ToF). There are new emerging technologies to improve the performance of ToF LiDAR units. On the other hand, frequency-modulated continuous-wave (FMCW) is often seen as an alternative technology of ToF. While FMCW has performance advantages, the complexity difference between FMCW and ToF options is vast, creating a cost challenge.
Focus on miniaturization
In order to adopt FMCW into the automotive LiDAR industry, it could prove instrumental in addressing miniaturization requirements. Derived from the safety accessories already in use on later model vehicles, FMCW’s continuous-wave operation avoids the eye hazards of high peak powers often limiting pulsed LiDAR ranges. Additionally, FMCW’s sensitivity exceeds what’s feasible with direct detection, often resulting in better performance.
“We think Si (silicon) photonics is high affinity technology to the FMCW LiDAR for miniaturization,” says Kyocera’s Mahiro Tsujino (Technology Marketing Manager; [email protected]). “Over the last 15 years, Kyocera has been supporting the fiber-optic communication industry by providing the ceramic packaging solution to enable Si photonics miniaturization. As a developer of ceramic package solutions for the long-range detection, high resolution, and miniaturization required for laser devices, Kyocera is experienced at providing support from prototypes to volume production. Kyocera can combine different technologies to provide the packaging solutions to satisfy challenging requirements.”Of course, the Si photonic IC device requires challenging thermal management and complicated optical alignment with a scanner during the assembly process. Thermal management is especially crucial considering the varying and often harsh operating environments for today’s vehicles. The size reduction, heat dissipation, and lower inductance levels found with ceramic packaging provide an attractive solution to conventional alternatives.
“While LiDAR module manufacturers are working on integration of LiDAR modules, ceramic packaging technology will enhance the evolving miniaturization by providing customized design solutions regardless of the laser transmission technology. More adoption and broader implementation will lower the cost,” says Tsujino.
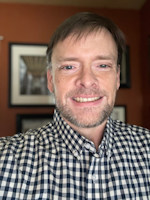
Peter Fretty | Market Leader, Digital Infrastructure
Peter Fretty began his role as the Market Leader, Digital Infrastructure in September 2024. He also serves as Group Editorial Director for Laser Focus World and Vision Systems Design, and previously served as Editor in Chief of Laser Focus World from October 2021 to June 2023. Prior to that, he was Technology Editor for IndustryWeek for two years.
As a highly experienced journalist, he has regularly covered advances in manufacturing, information technology, and software. He has written thousands of feature articles, cover stories, and white papers for an assortment of trade journals, business publications, and consumer magazines.