SPECIAL REPORT: Photonics and the energy crisis
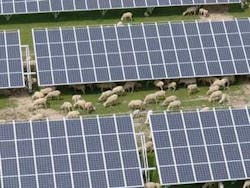
GAIL OVERTON, Associate Editor
Unlike prior energy crises in 1973 and 1979—which eventually faded as oil prices stabilized and political tensions eased—today’s crisis is viewed by many as a permanent economic and political “affliction” that can be solved only by finding sources of renewable, clean energy. This view is echoed by many energy experts, such as Matthew Simmons, chairman and CEO of energy investment banker Simmons & Co. International (Houston, TX) and author of Twilight in the Desert: The Coming Saudi Oil Shock and the World Economy. “Whether or not the world’s oil production has peaked isn’t really relevant,” said Simmons. “What’s important is that demand will soon outstrip supply. We need to embrace alternatives like solar and grow its infrastructure by astonishing amounts.”
Energy consumption
In the report Key World Energy Statistics 2005 from the International Energy Agency (Paris, France), oil consumption in 2003 accounted for 42.6% of the total energy used worldwide. While renewable combustibles (ethanol from crops, for example) account for an encouraging 14% of energy consumption, solar, wind, and geothermal power represent only 3.5% of total energy consumption.
Breaking fossil-fuel dependence
Today, photonic solutions to the energy crisis—often viewed only as solar power—represent just one facet of a multifaceted approach to the problem. Clearly, oil is here to stay until the infrastructure for alternative fuels and power sources is in place. But in addition to solar power, photonics can play a significant role in reducing energy consumption through solid-state lighting and other energy-efficient devices.
Solar photovoltaic technology continues its march as a promising renewable energy source. By 2010, solar-cell manufacturers such as Sanyo Energy (San Diego, CA) plan to develop hybrid solar cells with ultrathin amorphous-silicon layers that can reach conversion efficiencies of 22%—a noteworthy achievement compared to the current 10% to 15% for the best silicon-based technology. More manufacturable and cost-effective photovoltaic technologies, including polymer, photochemical, and even quantum-dot solar cells, have reached conversion efficiencies near 11% (see www.laserfocusworld.com/articles/252486). But even the largest silicon-based photovoltaic concentration in the world—Germany’s Pocking solar park, which generates 10 megawatt hours (MWh) of solar energy each year (see figure)—accounts for only 0.000012% of the world’s total yearly energy consumption.
Although the prospect of building enough solar parks to meet energy needs may not seem feasible, Martin Bucher (www.martin-bucher.de), the developer and principal engineer of the Pocking solar park, is more optimistic. “Ten to fifteen thousand times more energy than the world uses today falls on Earth’s surface in the form of free sunlight—an energy source that suffers none of the risks brought about by Middle East oil dependence, terrorism directed at a nuclear facility, or the global-warming consequences now at the forefront of our concerns,” says Bucher. An analysis by John Turner, principal scientist at the National Renewable Energy Laboratory (Golden, CO) shows that the electricity needs of the U.S. could be met by a 100 × 100-mile-square photovoltaic array in Nevada with even 10% conversion efficiency.3
Government and private funding is now shifting away from photovoltaic research and development and toward industry partnerships and alliances to accelerate commercial acceptance of photovoltaic technology (see “Catching up with the plant kingdom”). The engine that powers photosynthesis—the Sun—may power a new generation of transportation vehicles and all of the functions in our homes through rooftop photovoltaics.
Solid-state lighting has the potential, like solar energy, for widespread implementation as more manufacturers convince their customers of its energy-saving merits. A recent Optoelectronics World supplement published by Laser Focus World explored solid-state lighting developments, including better thermal management for improved efficiency, LEDs for white-light applications, and even nanosize light-emitters (see www.laserfocusworld.com/articles/250414, www.laserfocusworld.com/articles/250400, and www.laserfocusworld.com/articles/250408). Other energy-saving photonic technologies include laser televisions, organic lighting devices, and new methods of concentrating light to put it exactly where it’s needed (see “Better lighting makes energy count”).
Optical sensors are playing a role in extending the amount of available energy resources by increasing the amount of oil that is extracted from existing wells (see “Optical sensors enhance oil and gas yields”).
Future photonics advances may hold the greatest potential for addressing the energy crisis. Harnessing “free” electricity from the National Ignition Facility’s (www.llnl.gov/nif) Inertial Confinement Fusion program may seem farfetched, but it does offer a ray of hope that a long-term solution may eventually emerge from the minds of our best photonic scientists as the quest continues for a sustainable energy future.
REFERENCES
1. J.R. Petit et al., Nature 399, 429 (1999).
2. www.cru.uea.ac.uk/cru/press/2005-12-WMO.pdf; further information by Tim Osborn and Keith Briffa, Science 311, 841 (Feb. 10, 2006).
3. J.A. Turner, Science 285, 687 (July 30, 1999).
Catching up with the plant kingdom
HASSAUN JONES-BEY, senior editor
When one considers that a very large and nearby nuclear-powered, blackbody photon radiator, commonly known as “the Sun” either directly or indirectly powers every process on Earth—including “renewable” wind and geothermal energies, as well as the production of fossil fuels that are being consumed faster than they can be renewed—the question becomes: Energy crisis? What energy crisis? Humankind is constantly bathed in orders of magnitude more energy than we could possibly use. In fact, the worldwide energy crisis seems to have a lot less to do with shortages than with learning to negotiate our abundantly life-sustaining sea of photonic energy in ways that can be less toxic to our own continued existence.
The plant kingdom appears to be ahead of humanity in this regard. Two-dimensional femtosecond IR spectroscopy studies of the photosynthesis process at Lawrence Berkeley National Laboratory (Berkeley, CA) indicate that Mother Nature has developed a far more efficient method for harvesting light in photosynthesis than humans have in solar cells (see www.laserfocusworld.com/articles/231742). But humanity is taking steps to close the gap.
In addition to solar-cell technology, which converts sunlight directly to electricity using the photovoltaic effect, R&D at the U.S. Department of Energy (DOE) National Renewable Energy Laboratory (Golden, CO) in collaboration with academia and industry includes concentrating-solar-power technologies that generate electricity indirectly. These technologies include mirrors to concentrate solar radiation and heat a fluid that can then drive an electrical generator; passive solar heating and lighting of buildings; active and passive solar water heating; and solar ventilation, process heating, and air conditioning for industrial and commercial buildings (see Fig. 1).1In July, the National Institute of Standards and Technology (NIST; Gaithersburg, MD) began a 15-month research project at its new Roof Photovoltaic Test Facility to monitor the electrical and thermal performance of seven different photovoltaic (PV) roofing products that are designed to be integral parts of the roof and provide electricity and shelter from the elements. The NIST project is examining residential systems designed for sloped roofs and commercial building units designed for flat industrial roofs. Ultimately, the project is intended to provide PV users with a new generation of simulation models developed or validated with NIST data that will be useful in any given geographic location, building orientation, and with any photovoltaic-cell technology.2
A good bit further away from practical use (with the notable exception of providing electrical power for spacecraft), photonic energy—both PV and thermal PV—continues to be explored for transportation applications. A high school team named Sundancer from the Houston Vocational Center (Houston, MS) claimed its sixth consecutive win at the Dell-Winston Solar Car Challenge this summer. The challenge is an annual solar race for high schools hosted by The Winston School in Dallas, TX. The Sundancer team, powered by an array of Schott solar cells, completed 392 laps around the Texas Motor Speedway at an average speed of 29.5 miles per hour (see Fig. 2).Researchers at the Massachusetts Institute of Technology (Cambridge, MA) are exploring the use of thermophotovoltaic systems to power an automobile’s auxiliary functions, such as air conditioners, lights, and audio systems. And in Europe, the Technical University of Delft (Delft, the Netherlands) won the first-ever Frisian Nuon Solar Challenge, a six-day, 137-mile solar-boat race along canals and lakes in Friesland, a northern province in the Netherlands.
In October, a national renewable energy conference, hosted by the DOE and the U.S. Department of Agriculture at the America’s Center in St. Louis, MO, will focus on the advanced energy initiative (AEI) announced by President George W. Bush last February. The AEI includes a $148 million Solar America Initiative (SAI) in the 2007 budget—an increase of $65 million over the FY06 budget—intended to accelerate the development of solar technologies, such as photovoltaics and concentrating-solar-power systems, for generating electricity.
The stated goals of SAI are to achieve market competitiveness for PV by 2015 through government partnerships with industry, universities, national laboratories, states and other public entities; and to achieve market competitiveness for CSP by 2020 through ongoing and new R&D activities.3
The Solar America Initiative will also shift the focus of the current DOE Solar Energy Technology Program from solar-energy R&D focused on technology improvements to “funding industry partnerships and alliances to accelerate market-ready PV using aggressive cost goals, down-selects, and a new focus on eliminating manufacturing and production barriers.” SAI will also engage in “activities that address marketplace barriers and offer the opportunity for market expansion.”
The U.S. photovoltaic industry faces strong international competition (see www.laserfocusworld.com/articles/219784). So a primary objective of SAI will be to bolster the role of PV in the U.S. economy and in the national energy supply, which appears to already be coming to pass. In a business panel discussion during the 2006 CLEO/QELS & PhAST conference in Long Beach this May, John Dexheimer, a partner of First Analysis Private Equity and president of LightWave Advisors, noted that there have been at least 30 solar-cell public offerings in the last 10 months.
REFERENCES
1. www.nrel.gov/solar/
2. www.bfrl.nist.gov/863/bipv/roof.htm
3. www1.eere.energy.gov/solar/solar_america/index.html
Better lighting makes energy count
JOHN WALLACE, SENIOR EDITOR
Thanks to electrical lighting, the day has no end. We sleep fewer hours each night than our Victorian Age ancestors; we can stroll through a convenience store at 2 a.m. or work a shift that ends at dawn; and at home, we bathe in the light of a TV or computer screen at any hour of our choosing. Retail spaces are often overilluminated; car dealerships cast a nighttime glow for miles. About 22% of all the electrical energy produced in the U.S. goes into lighting—a figure ripe for reduction. But people are loathe to change their habits; so, then, how are we going to light our lives more efficiently?
One straightforward approach is to improve the technology. Most efforts to improve lighting efficiency are bent on boosting the number of lumens per watt (lm/W) that a light source is capable of emitting. While the efficiency of ordinary incandescent bulbs hovers at around 15 lm/W, tube-type fluorescent lamps can reach 80 lm/W. Compact fluorescent bulbs—the closest thing to a revolution in home lighting in decades—approach 60 lm/W.
The much-publicized light-emitting diode (LED) has come a long way since it was first conceived in its white-light form in the 1990s. While the earliest commercial versions, produced by Nichia (Kaminaka, Japan), emitted on the order of 10 lm/W, Nichia is now marketing a 100 lm/W white LED—although it is a small, indicator-light-size device. Nichia, Cree (Durham, NC), and Lumileds (San Jose, CA) are all developing more-relevant high-brightness white LEDs with efficiencies on the order of 50 lm/W (but at a cost still much higher than compact fluorescents). And, to give a flavor of where things are heading, Cree has demonstrated a record efficiency of 131 lm/W in a prototype cool-white LED chip running at 20 mA.
But there’s more to the story than improving the conventional inorganic LED. Many routes to lighting efficiency exist, ranging from other innovative sources to better lighting design.
OLEDs enter the high-efficiency realm
Best known for their use as displays in some cell phones, organic LEDs (OLEDs) can take the form of large panels no thicker than cardboard—a shape ideal for room lighting (see www.laserfocusworld.com/articles/206959). At one time, white-light OLEDs were like the early white LEDs—attention-getting, but dim and inefficient; years of research have since brought the promise of glowing walls and ceilings closer to reality.
In 2005, researchers at Universal Display (UDC; Ewing, NJ) unveiled a 6 × 6 in. white-OLED panel that emitted 100 lm at a 30 lm/W efficiency with outcoupling enhancement (a bonded glass plate that collected additional light), and 18 lm/W without enhancement (see Fig. 1).1 The device comprised narrow red-, blue-, and green-emitting OLED stripes, each with seven serially connected OLEDs. Electroluminescent dopants and four organic-thin-film layers permitted an external quantum efficiency of 20% for the red and blue stripes—but at a relatively low brightness.This year at SPIE’s Optics and Photonics 2006 (Aug. 13-17; San Diego, CA), Universal Display researchers presented their newest device—a small (25 cm2) white phosphorescent OLED, containing a single multidoped emitter (rather than stripes), which reaches a 31 lm/W efficiency with no outcoupling enhancement. At least as significant is the fact that the device achieves this efficiency at a commercially viable brightness of 850 nits. Adding outcoupling enhancement could boost its efficiency to near 50 lm/W.
Janice Mahon, vice president of technology commercialization at UDC, notes that these are two of several OLED-lighting approaches at UDC that are partially funded by the U.S. Department of Energy (DOE). While the red and green phosphors in UDC’s latest device are very long-lived, the blue needs further work, she says; although a light-blue phosphor with a 100,000-hour lifetime has been developed, it is not deep enough in hue. Further research will also push the device’s color-rendition index (a measure of “whiteness”), currently 70, to above the commercially desirable 80.
The lighting-OLED technology roadmap developed by the Optoelectronics Industry Development Association (Washington, D.C.) and the DOE calls for reaching OLED efficiencies of at least 120 lm/W (see http://lighting.sandia.gov/Xlightinginit.htm); the UDC researchers believe that improvements in external quantum efficiency may lead to 100 lm/W white OLEDs within five years. Mahon adds that the very different LED (directional) and OLED (diffuse) lighting technologies are natural complements.
Putting lumens where they’re needed
One elegant way to cut lighting energy needs is to use well-designed optics to put light just where it’s required. While reflectors are nothing new, refinements in optical design are resulting in fixtures that shun the simple approach of overillumination, instead creating pools of light that have just the right size and intensity profile for the job.
Larry Boxler, an optical engineer at Breault Research Organization (BRO; Tucson, AZ), mentions automotive, task-specific (such as spotlights), and general illumination as three areas of concentration. For example, a typical incandescent automotive stop lamp requires around 35 W of electrical power, but a single LED running at 3 to 5 W can be used to meet the same requirements. “Because of the characteristics of the LED, this can only be accomplished by using specialized optics to efficiently capture the light from the LED and direct it into the pattern,” he notes. “The energy savings can be especially important on electric vehicles” (see Fig. 2).For general lighting, the flexibility in customizing the light pattern from LEDs is significantly greater than for standard fluorescent tubes, says Boxler. Even compact fluorescents are large and diffuse when compared to LEDs, highlighting the superiority of high-efficiency LEDs and optics for a myriad of uses requiring directional lighting, ranging from museum displays to home-accent fixtures.
Laser TV may pay for itself
All home lighting sources can benefit from an efficiency boost, including the developed world’s most common living-room light fixture—the TV. While the cathode-ray tube is now on the way out, its replacements (plasma, liquid-crystal display, and projection) are, by and large, similar energy hogs.
A 55 in. plasma TV consumes about 750 W of electrical power, says Aram Mooradian, chief technical officer of Novalux (Sunnyvale, CA). Such a power draw nears that of toasters and microwave ovens, but has far more impact because TVs are on for about eight hours a day on average. Novalux has been developing a projection TV based on its core technology, an extended-cavity surface-emitting laser. The cavity results in a TEM00 optical power high enough to produce frequency-doubled light from an intracavity lithium niobate crystal at conversion efficiencies of 50% to 70%. Blue-, red-, and green-emitting sources produce 100 mW or more each and are used in arrays to produce multiwatt outputs per color (see www.laserfocusworld.com/articles/248114).
The power-conversion efficiency of the lasers is currently 6% (10% is the target); along with the pure colors, this makes for a bright, low-power display. For example, a 55 in. TV based on the Novalux lasers would consume only about 200 W, according to Mooradian. At eight hours a day of viewing, this would amount to a savings of 1606 kWh per year or, at the 12-cents-per-kWh standard for California, a yearly savings of $193. For a $1500 laser TV (the target price at high-volume production), the electrical savings would pay for the TV in 7.8 years, says Mooradian. In Japan, where electricity costs up to 30 cents per kWh, the cost-recovery time would drop to just over three years.
REFERENCES
1. B. D-Andrade et al., Proc. SPIE 5937, (2005).
2. B. D-Andrade et al., Proc. SPIE 6333 (2006).
Optical sensors enhance oil and gas yields
KATHY KINCADE, CONTRIBUTING EDITOR
Pull up to a gas pump these days and you will quickly be reminded how emotional an issue the energy crisis can be. But behind the annoyance and even anger many feel when it comes to the price of gasoline or the monthly energy bill are some alarming facts:
- The world’s 120 largest oil fields produce about 50% of the world’s crude oil supply (33 million barrels per day); however, only 60 oil fields in the world produce more than 100,000 barrels/day (see Fig. 1).
- Only 20% to 30% of available reserves are currently extracted from existing wells.
“Right now we only get about 30% of the reserves,” said Paul Sanders, who oversees technology acquisitions at Weatherford International (Houston, TX), a leading systems integrator in the oil and gas industry. “Oil is mixed in with sand and you have to do a lot of things to ‘herd’ it toward the producing well. Eventually you hit water and other things where it becomes no longer viable and too costly to separate out. But optical technology promises to increase the yield. Maximizing reserves is a big deal today, even more so than just a few years ago because of the growing thirst for oil worldwide. New oil fields are billion-dollar projects, so there is also a value proposition; increasing the recovery factor even by a couple of percentage points can translate into huge profits.”
In terms of production, the oil industry can be segmented into three main markets: deepwater (subsea), platform, and land. Subsea fields are the largest oil producers (100,000+ barrels per day) but have the fewest number of wells (in the hundreds). Platform wells number in the thousands worldwide and produce around 10,000 barrels per day. Land-based wells far outnumber the others (tens of thousands) but are the lowest producers (a few hundred barrels per day).
Contrary to popular perception, most oil is not obtained from single, vertically oriented production wells. Instead, most oil fields operate deep beneath the earth and sea, ultimately feeding dozens of production wells on the surface. With the advent of directional drilling 20 years ago, many fields are a series of horizontal wells that play off a single vertical well, much like a wagon wheel with spokes. The oil does not lie in large, easily accessible liquid pools; more often it is in near-solid form, tucked away in nooks and crannies spanning miles of dirt, sand, and rock. Locating these pockets with the use of seismic techniques and extracting this oil is what drives the high costs of oil production.1
“Two thirds of the world’s oil reservoirs are heavy oil that is ‘stuck’ and has to be heated to get it out of the ground,” said Clemens Pohl, business development manager for the Photonic Measurement Division of Agilent (Palo Alto, CA). “In a reservoir you might have several injection wells pumping in pressurized hot steam (200ºC to 300°C). Steam heats and liquefies the oil, which floats up to the production well and is pumped out. The key is to know where to inject the steam, the required flow volume per zone, and whether any cold-water breakthrough is cooling down the heated oil.”
This is where optical sensors come in. By providing continuous multipoint pressure and temperature data, oil providers can better optimize well production and, theoretically, increase output and reduce costs. Optical components offer key advantages over electromechanical components in the field, including longer lifetimes, greater accuracy, lower cost, and the ability to withstand the often hot and wet conditions found in a production or injection well. This last feature alone opens up whole new oil-discovery and management applications such as towed arrays and sea-bottom monitoring systems.
“Offshore, when looking for reserves or trying to figure out what is going on in a field, they tow 16 to 20 cables with electromechanical sensors behind a boat and fire off an air gun to get pictures of what is going on underwater. The cables are very large, the risk of damage is high, and the cost is very expensive—$500,000 to $1 million a day to operate,” said Pat Edsell, president and CEO of NP Photonics (Tucson, AZ), supplier of single-frequency fiber lasers (1550 nm, less than 3 kHz linewidth) for platform-, pipeline-, and boat-based monitoring systems. “So people are working to develop all-optical towed arrays where the only things in the water are passive devices. Same with sea-bottom monitoring; the goal is to put a grid of optical fibers and sensors on the ocean floor to cover an entire reservoir (10 to 20 wells) and monitor the reservoir on a real-time basis. With this kind of active monitoring, people in the oil industry believe they can double the amount of reserves that are recovered.”
Intelligent wells
For years the conventional approach to monitoring production wells has been to use a “slick line” with several electromechanical sensors and drop the line every 10 meters to create a profile of the well and its contents. But advances in optical technologies—including multipoint fiberoptic sensors and interferometric flow controls—are enabling the oil industry to take a more “intelligent” approach to well management. For example, Weatherford’s initial optical product was a single-point optical pressure sensor that utilizes Bragg gratings operating at 1550 nm; today the company also sells a distributed temperature sensor and a multiphase in-well optical interferometric flow meter that measures the flow and constituency of the fluids at strategic points. Other optical pressure- and temperature-sensing technologies include evanescent field, fluorescence, intensity modulated, magneto-optic, and polarization.
“The ultimate is in-well seismic, which gives you an acoustic ‘snapshot’ of reservoirs in real time as they are being depleted,” Sanders said. “Until recently we placed seismic systems on the surface, set off an acoustic charge, then measured the acoustic signal. But there is a lot of distortion with this approach. Permanently positioning optical sensors within the well and doing cross-well tomography is much more powerful, although this is in the early stages.”
Nonlinear distributed temperature sensing (DTS) is proving to be one of the most attractive choices, especially for downhole monitoring. In a typical installation, a DTS system is located in the instrument area of the platform or subsea control module (no active components go downhole). A hydrogen-tolerant cable is then placed down inside the production tubing, and a passive optical system featuring a broadband light source with a tunable filter is lowered into the hole (see Fig. 2). Light (1064 to 1550 nm) is then transmitted down the cable, with the resulting reflection spectrum detailing changes in pressure and temperature data inside the well.Agilent is looking to capitalize on the growing interest in DTS via its new Fiber Sensing business segment combining its expertise in photonic-test and optical-time-domain-reflectometry technologies with a lower-cost plug-and-play approach. Combining standard 1064 nm diode lasers in an integrated “optoelectronic building block” eliminates the need for cooling.
“The hermetically sealed package is filled with inert gas, which protects the critical components so they can withstand shocks, vibration, and temperature changes,” said Pohl. “So there are fewer components, fewer reasons for failure, and long-term stability. The oil industry is most interested in long-term comparable information, so we focused our efforts on extended operating conditions, low power consumption, reliability, and ruggedness.”
Sabeus (Calabasas, CA) is taking a slightly different approach with its interferometric optical sensor system, using distributed-feedback diode lasers and a proprietary multivariable control system that improves the laser’s frequency stability and reduces the phase noise, according to the company. “We produce fiberoptic pressure and temperature-monitoring systems for in-well deployment that enhance extraction from existing wells by providing the real-time data on downhole conditions that allow operators to make efficient decisions concerning steam injection, water flood, or CO2 injection,” said Al Garden, vice president of operations at Sabeus. “Real-time monitoring allows maximum reservoir exploitation while minimizing the risk of destabilizing the formation.”
Distributed temperature sensing is also being used to optimize the electrical power grid in times of stress (see “Distributed temperature sensors find ‘missing’ power,” p. 78).
REFERENCE
1. T. Knott, “Listening with Light,” www.OilOnline.com, April 2003.
Distributed temperature sensors find ‘missing’ power
Whether due to global warming, cyclical weather patterns, or a combination thereof, 2006 saw record temperatures (highs and lows) around the world—a growing trend so far this decade. Peak usage of electronic appliances (air conditioners/heaters) can put significant stress on the electronic power grid in major metropolitan areas and entire regions.
Optical sensing systems are beginning to play an important role in enabling service providers to better manage the flow of electricity in peak usage situations. Distributed temperature sensing can provide continuous monitoring of high-power cable temperatures-detecting hot spots, delivering operational status, and providing power-circuit rating data to avert potential outages by ensuring the cables do not exceed the maximum allowable temperatures. The sensing fiber is either embedded in the power cable or deployed along the outside of the cable. It is intrinsically immune to electromagnetic interference and provides reliable temperature measurements.
“Power outages are due to the capacity of the power cables and the utility providers are limited by the temperature of the power cable,” said Clemens Pohl, business development manager for the Photonic Measurement Division of Agilent (Palo Alto, CA). “They want to be able to consistently measure the cable temperature and increase the utilization as needed. This is especially important in the United States, China, India, and other countries where the power infrastructure is underdesigned.”
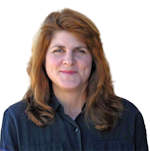
Gail Overton | Senior Editor (2004-2020)
Gail has more than 30 years of engineering, marketing, product management, and editorial experience in the photonics and optical communications industry. Before joining the staff at Laser Focus World in 2004, she held many product management and product marketing roles in the fiber-optics industry, most notably at Hughes (El Segundo, CA), GTE Labs (Waltham, MA), Corning (Corning, NY), Photon Kinetics (Beaverton, OR), and Newport Corporation (Irvine, CA). During her marketing career, Gail published articles in WDM Solutions and Sensors magazine and traveled internationally to conduct product and sales training. Gail received her BS degree in physics, with an emphasis in optics, from San Diego State University in San Diego, CA in May 1986.
Hassaun A. Jones-Bey | Senior Editor and Freelance Writer
Hassaun A. Jones-Bey was a senior editor and then freelance writer for Laser Focus World.
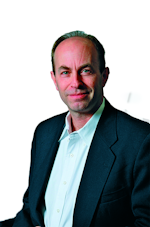
John Wallace | Senior Technical Editor (1998-2022)
John Wallace was with Laser Focus World for nearly 25 years, retiring in late June 2022. He obtained a bachelor's degree in mechanical engineering and physics at Rutgers University and a master's in optical engineering at the University of Rochester. Before becoming an editor, John worked as an engineer at RCA, Exxon, Eastman Kodak, and GCA Corporation.
Kathy Kincade | Contributing Editor
Kathy Kincade is the founding editor of BioOptics World and a veteran reporter on optical technologies for biomedicine. She also served as the editor-in-chief of DrBicuspid.com, a web portal for dental professionals.