LASER AIRCRAFT DEFENSE: Homeland Security broadens search for technology to protect planes
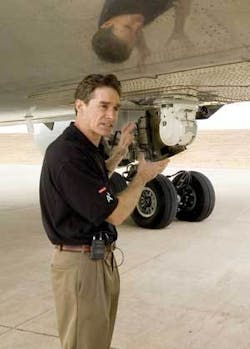
The Department of Homeland Security (DHS) is hedging its bets on technology to protect civilian airliners from attack by shoulder-launched missiles. The leading candidate remains Directed Infrared Countermeasures (DIRCM)-mid-infrared lasers deployed on planes to blind the missiles’ infrared seekers (see www.laserfocusworld.com/articles/204109). But, as directed by Congress, the DHS is issuing multiple exploratory contracts for other approaches. Among the contenders are ground-based lasers and microwave systems installed near airports.
While DIRCM systems originally were developed to protect military aircraft, the terrorist threat led the DHS to study adapting the technology to protect large civilian airliners. In 2004, the DHS awarded a pair of $45 million, 18-month contracts to demonstrate that DIRCM technology can defend civilian airliners. Both BAE Systems (Nashua, NH) and Northrop Grumman’s EO/IR Countermeasures Group (Rolling Hills, IL) succeeded in adapting their military systems to meet the goals of the phase 2 DHS contracts.
However, a DHS spokesman says the agency has found “they do need much further testing in operational environments.” Major airlines are worried about costs of the equipment and of operating and maintaining it. A report issued last year by the Rand Corporation (Santa Monica, CA) warned that maintenance requirements could pose additional problems. The mean time between failures of military DIRCM systems is only several hundred hours, which could lead to unacceptable down times for civilian airliners. Fuel efficiency is another concern. The DHS is awarding phase-3 contracts to both BAE and Northrop to work out those issues.
Laser blinds missile sensors
The contractors each teamed with airlines for the phase 2 demonstrations. “We didn’t have a lot of experience with the commercial airline industry,” says Steve duMont of BAE. Military DIRCM systems are mounted in external pods, which increases drag. Airlines worry much more about fuel efficiency, so BAE moved most of the system inside the airplane. Infrared and ultraviolet sensors must be outside the plane to spot missiles; combining the two bands gives “a very strong discrimination against false alarms,” he says. The beam from a diode-pumped optical parametric oscillator emerges from a jamming head on the bottom of the plane, which moves to track the missile (see figure). The OPO emits in five bands between 1 and 5 µm to blind the various sensors that heat-seeking missiles use to home in on aircraft engines. Northrop’s system is similar.
Developers say they’ve addressed many issues cited by Rand. To increase operating life, the BAE system goes into sleep mode when the plane is on the ground or at elevations above the 15,000 to 20,000 ft range of shoulder-launched missiles. The mean time between failures is nearing 2000 hours of operating time, and by the end of phase 3 duMont hopes to reach 4800 hours, well above the DHS’s 3000-hour target. Moving most of the equipment inside the plane reduced extra drag, which the DHS wants to be less than 1%. The DHS also wants to keep fly-away cost to $1 million per plane for the 1000th plane equipped, a goal BAE says it can reach.
The Rand report did not mention what duMont calls “a really big challenge”-controlling access to the critical military DIRCM technology, which must be addressed if equipped airliners fly overseas.
Advocates of stationary ground-based systems say they can protect more planes at lower cost. Instead of putting a laser and detection system on each plane, ground-based systems would install one system to cover an entire airport. Such systems have been developed for military bases, and could protect all incoming and outgoing aircraft, not just the big passenger jets targeted for DIRCM. This year, DHS will spend a little under $10 million on phase 1 contracts to develop detailed plans.
One contender is the Vigilant Eagle system developed by Raytheon Missile Systems (Tucson, AZ). Passive infrared cameras spot and track missiles, feeding information to a command and control center. A billboard-size scanned-array microwave antenna targets missiles. The microwave beam seeps into the missiles through vents and seams, interfering with the control system. The microwave beam doesn’t have to hit the missile as precisely as a laser, and has demonstrated kills with live missiles, says Raytheon spokesman Alan Fischer. The frequency is chosen so it does not interfere with aircraft-control systems, so nearby planes would not be affected.
Another contender is Skyguard, built by Northrop Directed Energy Systems (Los Angeles), based on the deuterium-fluoride chemical laser technology used in the Tactical High-Energy Laser (THEL) jointly developed by the U.S. and Israel. THEL shot down targets from mortar rounds to Scud missiles in tests at the White Sands Missile Range. Skyguard is one-quarter the size of the THEL testbed, but can deliver more power, says Northrop spokesman Bob Bishop. It would be assembled from three modular units, each about 20 feet long, with one containing enough chemical fuel to fire 20 times. Refueling takes about half an hour. The system can defend an area 10 km in diameter, and Northrop says they could deliver one 18 months after receiving an order.
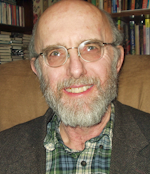
Jeff Hecht | Contributing Editor
Jeff Hecht is a regular contributing editor to Laser Focus World and has been covering the laser industry for 35 years. A prolific book author, Jeff's published works include “Understanding Fiber Optics,” “Understanding Lasers,” “The Laser Guidebook,” and “Beam Weapons: The Next Arms Race.” He also has written books on the histories of lasers and fiber optics, including “City of Light: The Story of Fiber Optics,” and “Beam: The Race to Make the Laser.” Find out more at jeffhecht.com.