MICROSTRUCTURED FIBERS: Anamorphic fiber circularizes elliptical beams
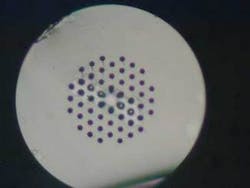
For many applications, the elliptical beam emitted by a typical edge-emitting laser diode would be far more useful if it were circular. Reshaping a laser-diode beam is normally the province of anamorphic optics such as pairs of cylindrical lenses or prisms. However, a section of single-mode optical fiber with a core that changes shape in the right manner along the fiber’s length could do the same thing. But, except for fiber drawing, which produces a smooth change in core diameter while keeping the shape of the core the same (and is thus useless for beam-circularizing), no easy way has existed to create a position-dependent variation in the core of a clad fiber.
Researchers at the University of Bath (Bath, England) have changed all that by taking a microstructured optical fiber and pressurizing some air channels so that they partially inflate, then heating and drawing a section of the fiber, with the result that the fiber’s central solid core varies from approximately circular to elongated (and back) with position. Other more-complex transitions have also been demonstrated. The researchers have also developed a second technique based on controlling the surface tension of the heated glass.The fiber starts out with a hexagonal array of uniform-size holes; one central hole is absent, defining a single-mode core. In the pressure-fabrication method, the researchers plug certain holes at one end of the fiber with glue (see figure), as well as all the holes at the other end. The open holes are pressurized with dry nitrogen at 5.3 bars pressure and a central portion of the fiber’s length heated to soften the glass; the heated portion is then drawn and tapered. The pressurized holes in the heated section collapse the unpressurized holes; the smooth transition from unheated to heated portions of the fiber creates an adiabatic (beam-quality-conserving) core transition. The fiber can then be cleaved somewhere in its altered portion.
Many uses possible
If a few holes in a line are collapsed, the resulting fiber changes a circular input to an elliptical output, or the reverse. If just one adjacent hole is collapsed, the result is a fiber with geometry-induced birefringence (a beat length on the order of 0.4 mm in one experimental example). More-complex transitions are also possible; the researchers collapsed five holes in a ring (with the original solid core forming the sixth ring element) to create an adiabatic transition to the lowest-order ring-shaped mode. Such a mode may be valuable for applications such as optical trapping. An adiabatic transition from a one-array-element to a seven-element solid core results in a beam expander.In the other hole-collapsing technique, which relies on surface tension, the holes in the starting array are made nonuniform in size; when heated, the larger holes expand relative to the smaller ones, with no hole-plugging required. Each technique has its advantages, says Tim Birks, one of the researchers.
“I would say that the surface-tension method is harder to control, because the core shape is determined by the degree of (relative) hole deformation, whereas in the hole-plugging method all you have to ensure is that the selected holes have collapsed,” he notes. “Using pressure you can’t ‘overcollapse’ the holes, but using surface tension you can ‘overdeform’ them. Also, using surface tension you’d need to design and make the starting fiber specifically to suit the application. However, given a uniform supply of suitable fiber and a process of controlled time, temperature, and pressure (established by trial and error perhaps), I don’t see why the surface-tension method can’t be made reproducible.”
The advantage of the surface-tension approach, says Birks, is the elimination of the hole-gluing step. “It’s not clear which method would be most economical overall,” he adds. “Let’s say surface tension for large volumes, and hole plugging for small volumes.”
Given the millions of edge-emitting laser diodes produced each year, the potential demand for an inexpensive beam-circularizing fiber pigtail could be large; Birks expects that such a pigtail would be a few centimeters in length. Birks mentions other uses for the Bath technology, including multicore fiber devices, fiber sensors (containing short multicore sections at defined places along the fiber), beam expanders for input and output coupling to highly nonlinear small-core photonic-crystal fibers, and mode converters. The Bath group has already created a fiber section that converts between the LP01 and LP02 fiber modes.
REFERENCE
1. A. Witkowska et al., Optics Letters 31(18) (Sept. 15, 2006).
About the Author
John Wallace
Senior Technical Editor (1998-2022)
John Wallace was with Laser Focus World for nearly 25 years, retiring in late June 2022. He obtained a bachelor's degree in mechanical engineering and physics at Rutgers University and a master's in optical engineering at the University of Rochester. Before becoming an editor, John worked as an engineer at RCA, Exxon, Eastman Kodak, and GCA Corporation.