PHOTONICS APPLIED: WEARABLE PHOTONICS: Smart photonic textiles begin to weave their magic
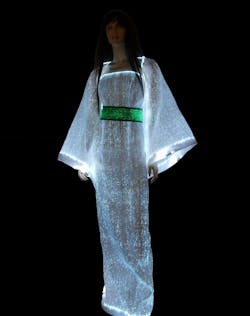
KUNIGUNDE CHERENACK, KOEN VAN OS, and LIESBETH VAN PIETERSON
While conventional electronic circuits are compact and have a high level of functionality, they are limited by the maximum substrate size available for processing, substrate rigidity, and fragility. It is impossible to fully integrate such electronic circuits into mechanically active environments such as clothing. Alternatively, smart textiles such as those based on organic light-emitting diodes (OLEDs) are a new step in the evolution of wearable photonics and represent the drive to integrate new functionalities into hitherto inaccessible surfaces for large-area sensing and illumination, despite some obvious integration challenges.
Engineers tend to evaluate OLEDs by the functionality of individual devices. Basic OLED technology research is driven by the goal of optimizing device performance, the fabrication process, device architecture, materials choices, and encapsulation. However, product designers experience OLEDs in a different way by thinking of them in terms of the "lighting experience" and "design aesthetics" when integrated into a larger system.1 Philips Research argues that it is necessary to rethink the way in which we carry out OLED research by including design-centered thinking.
Textile OLEDs—Displays of the future?
Photonic textiles represent a promising industry in which OLEDs could bring essential improvements in performance that may lead to groundbreaking new applications and products. The vision of replacing everyday textiles in curtains, furniture, and clothing with light-emitting fabrics will bring inert objects to life by integrating intelligence and visual feedback within the everyday objects that surround us.
Current photonic textiles are either based on integrating standard components such as LEDs with conductive yarns inside the textile or developing optoelectronic devices with a fiber form factor (such as photoluminescent polymer-coated fibers, surface- or side-emitting fibers, or yarns coated with thermo-chromic ink) that can be integrated directly into textile structures (see Fig. 1 and Fig. 2a).2-5, 8 The integration of OLEDs to create photonic textiles is an emerging trend by which researchers hope to combine the unique properties of textiles (breathability, comfort, low cost) with the beneficial properties of OLEDs (diffuse illumination, low energy consumption).The advantage of OLEDs, in comparison to the LEDs that are often used in textiles, is the emission of homogenous light over a larger surface area. In addition, feedback from designers shows that photonic systems enabled by OLEDs are aesthetically more pleasing than LED-based enhanced textiles that must be covered by additional textile optical diffuser layers.6-7 Compared to other fiber-based photonic systems such as textiles fabricated from photoluminescent, thermo-chromic, or optical fibers, OLEDs have higher light intensities. And finally, OLEDs are also lightweight, have a flat form factor, and can be flexible if fabricated on a polymer foil substrate.
Design challenges
Although flexible OLEDs seem a perfect choice for textile displays, they have significant issues that need to be overcome. One main issue is the OLED lifetime, especially for devices based on flexible foil substrates. So far, the best barrier layer for OLEDs is still a glass encapsulation layer, which unfortunately results in rigid OLEDs that are less suitable for textile integration.
While flexible OLEDs are not yet commercially available, designers have already started using available OLED devices by integrating them into demonstrator garments. Early adoption of OLEDs in couture garments, such as the figure-hugging catsuit worn by Fergie of the Black Eyed Peas during a recent concert tour in Paris9 (see Fig. 2b), clearly shows some of the mechanical integration challenges facing textile OLEDs. This garment shows that it is possible to design a comfortable OLED-based garment with exciting new lighting aesthetics. However, the stiffness of the OLED panels is still visible and remains a limiting factor in this type of garment design.
In general, concessions must be made to the textile qualities of the garment using today's OLED technology; these are not wearable outfits that you could use in daily life. The gap between desired lighting properties and textile comfort needs to be closed by further technology development.
Closing the gap
The aim of the EU PlaceIt project (www.place-it-project.eu/)—a Platform for Large Area Conformable Electronics for InTegration—is to develop highly conformable, large-area textile-based circuits with integrated OLED components. As a consortium member in the PlaceIt project, Philips Research is trying to ensure that the overall textile maintains its desirable properties of comfort, breathability, and bendability/stretchability.
As a first step, we are trying to establish whether or not we can improve on the conventional approaches to designing OLED textiles. Our vision is to attach rigid or flexible OLED tiles onto flexible or stretchable textile substrate demonstrators. Individual OLEDs will be connected using stretchable interconnects or conductive yarns to power individual lighting elements. Although the results are promising, early process feedback from designers indicated that we are not going far enough yet to meet the needs of the end user.
Clothing designers desire a much more subtle integration of lighting elements into textiles. We need to develop photonic textiles that are more like fabric in order to minimize the impact of the integrated lighting element on overall comfort and increase the aesthetics of the final design. What does this design need mean for OLED technology development? Is it possible to bring OLEDs even closer to the world of textiles?
Consider the possibility of developing OLED fibers that have textile characteristics. Integration of such OLED lighting elements would be subtle and could occur during the textile manufacturing process, eliminating the need to add the illuminating devices during a later step. One can envision an "OLED fabric" that could be shaped to meet the requirements of individual products or garments. These OLED fabrics would provide more design freedom and could be tailored to a variety of needs.
Another unique property of OLED fibers would be the ability to emit light along their whole surface area, and not just in one dimension like conventional planar, flat devices (as in Fig. 2b). Photonic textiles fabricated from OLED fibers would be three-dimensional, introducing a new modality for designers to play with. But is it possible to fabricate OLED fibers? The answer is yes.
Researchers have investigated the possibility of developing textile-compatible OLED fibers by fabricating OLED materials onto various types of yarns and fibers. Here the fiber geometry presents unique challenges in addition to the usual problems faced when fabricating OLEDs, such as finding suitable transparent electrode materials and suitable barrier layers.
These OLEDs can be fabricated to emit along the surface or along the fiber axis (see Fig. 3a). At Philips, optical fiber light-emissive structures suitable for both illumination and decorative objects were formed by manufacturing OLEDs on the outer surface of a glass fiber (see Fig. 3b). By using the natural cylindrical shape of the fiber and the sophisticated changes at refracting planes at the interior of the fiber, the light could be extracted more efficiently. Due to its reduced size and high flexibility, multiple arrangement of the light-emitting segments becomes possible, including integration into textiles or plastics, displaying artistic light effects (see Fig. 3c).Researchers in the Texoled project struggled to coat fibers with OLED layers that were sufficiently homogenous and could not achieve adequate adhesion between layers.10 Due to high surface roughness, they were not able to achieve light emission with their OLED fibers. At the University of Michigan (Ann Arbor, MI), however, light emission by textile OLED fibers was successfully demonstrated.11 A 1 mm segment of one of their OLED devices formed concentrically around a 480-μm-thick polyimide-coated silica fiber emitted green light under forward electrical bias. Light emission in this device occurs through the semitransparent outer electrode and the spread of the light emission is directionally independent. If this type of fiber could be fabricated in large quantities and made in a robust manner, it could enable three dimensional (3D), large-area light-emitting surfaces.
Commercial availability of OLED fibers that could be used to weave large-area OLED textiles would clearly unlock a wide range of new applications. However, many challenges need to be overcome before this possibility can be realized. In the short term, the concept of integrating more rigid OLEDs into conformable textiles remains the most promising route for future wearable photonic textile products.
REFERENCES
1. http://karinasiegmund.com/poeticrealismblog/
2. D. Graham-Rowe, Nature Photon., 1, 1, 6–7 (2007).
3. K.L. Yi Yang et al., Light-Emitting Diodes: Research, Manufacturing, and Applications IX, Proc. SPIE, Vol. 5739 (Mar. 7, 2005).
4. O. Shapira et al., Opt. Exp., 14, 9, 3929–3935 (2006).
5. http://material.media.mit.edu/?p=354
6. K.H. Cherenack et al., IEEE Electron Dev. Lett., 31, 7, 740–742 (2010).
7. www.photonics21.org/uploads/4Y4g2K7ElX.pdf
8. www.fashioningtech.com/profiles/blogs/gareth-pughs-unwearable-oled
9. http://community.lighting.philips.com/blogs/lighttalk/2011/08/11/the-black-eyed-peas-costume-designers-behind-the-scenes
10. www.mstonline.de/mikrosystemtechnik/smart-textiles/medien/2-Texoled_mst_Statustreffen_2009_Berlin.pdf
11. B. O'Connor et al., Adv. Mat., 19, 22, 3897–3900 (2007).
Kunigunde Cherenack, Koen van Os, and Liesbeth van Pieterson are scientists at Philips Research, High Tech Campus 5, 5656 AE Eindhoven, the Netherlands; e-mail: [email protected]; www.research.philips.com.