PHOTONICS APPLIED: MATERIALS PROCESSING: Laser additive manufacturing gains strength
Whether its called laser cladding, laser additive manufacturing, or additive layer manufacturing, the process of depositing material on a substrate using a laser, or creating an entirely new three-dimensional object by building up layers of material, is gaining strength in the materials-processing community. Because of the high level of interest, at least two new workshops were announced this year.1
Although applications using lasers and donor materials for component repair, surface patterning and strengthening, and rapid manufacturing have been under development for decades, laser additive manufacturing is just now gaining widespread industrial and commercial adoption. The reasons for increased adoption are similar to those for the growth in laser welding, including the advent of higher-power laser systems with tailored beam profiles, improved parts quality and longevity, as well as the increased need for environmentally sustainable engineering practices that reduce energy consumption, toxic emissions, and material waste.
Definition of terms and success
Cladding refers to adding a relatively thin layer (say, 3 or 4 mm) to the surface of an existing component to improve its surface properties, while additive manufacture (AM) is used for its mechanical properties and involves adding material to existing structures or building up material for freeform structures.
“Laser cladding includes application of corrosion-resistant materials to the inside of a pipe, for example, to protect the base material and avoid costly fabrication from expensive corrosion-resistant alloys,” says Stewart Williams, professor of welding science and engineering in the Welding Engineering Research Centre at Cranfield University (Bedfordshire, England), and chair of this year’s AILU Workshop. “Popular AM applications include repair of high-value components like turbine blades or engine seals, addition of high-performance material to the ends of turbine blades (called blade tipping), and for component fabrication. And because AM parts can be fabricated directly from CAD systems, each component can be easily changed to suit any requirement—particularly important in the medical applications such as implants.”
Laser AM is the area of greatest growth, according to Williams, with a large amount of research activity taking place in the U.K. and Europe. “In civil aircraft there is now extensive use of carbon fiber composite—up to 50% in the latest aircraft. The remaining metal is largely titanium to avoid corrosion issues,” he says “Standard manufacturing by machining components from solid billet typically puts 90% of the original material in the swarf bin. If AM is used, the amount of material waste is typically only 10%, and energy consumption and CO2 emissions are dramatically reduced—a recipe for success.”
James W. Sears, director of additive manufacturing at the South Dakota School of Mines & Technology (Rapid City, SD) and cochair of LIA’s workshop, points out that even though original parts manufacture may be an area for growth in laser AM, the real excitement is in high-volume applications such as ram-pipe cladding for oil drilling and for cladding repair and parts remanufacturing at large companies like Caterpillar (Peoria, IL). “We’re talking tons of material per month for many of these applications, unlike the perhaps single ton per year for prototyping and direct-manufacturing applications,” says Sears.
Cladding
All cladding applications involve flowing a powdered material through a nozzle or inserting/blasting a wire or donor material in the proximity of or directly into a laser beam. That material is then sintered or melted onto a secondary substrate and built up in layers through multiple passes of the laser.
Laser-assisted metal restoration and cladding includes laser-applied powder (LAP) and laser-applied wire (LAW) using lasers with power levels between 1 and 4 kW. “Hard facing materials like tungsten carbide in a nickel matrix are typical claddings that increase wear resistance of oil- and gas-drilling components, or for blades and cutting disks in agricultural applications,” says Christian Foehl, product manager at Trumpf (Ditzingen, Germany). “Compared to conventional coating technologies such as thermal spraying, laser metal deposition offers a real metallurgical bond that creates better coatings with higher resistance against common failures such as chipping. Using two or more powder hoppers to mix different types of powders together allows tailoring of the coating composition as needed,” he adds (see Fig. 1).
IPG Photonics (Oxford, MA) recently introduced 2, 3, and 4 kW lasers specifically for cladding, brazing, and annealing applications. And Coherent (Santa Clara, CA) offers its HighLight diode-laser system with 40% electrical-to-optical efficiency that delivers near-infrared light at either 808 or 975 nm with total output power in the multikilowatt range.
Rapid manufacturing
In powder-bed AM, a laser melts a layer of deposited powder into a 20 to 40 µm slice for direct metal laser sintering (DMLS) and 100 to 150 µm for selective laser sintering (SLS); additional powder is then deposited on top of each solidified layer and the process repeats, building the slices into a three-dimensional component. Both DMLS and SLS processes were pioneered by Electro Optical Systems (EOS; Munich, Germany). Functional polymer prototypes and aesthetic models as large as 700 × 380 × 580 mm3 can be built from nylon, glass-filled nylon, or polystyrene, and metal components as large as 250 × 250 × 195 mm3 can be produced from stainless steel, titanium, and other metals. 3T RPD (Newbury, England) uses these processes to develop custom components for a broad range of applications, from architectural models to dental implants (see Fig. 2). The company even designed modified SLS nylon parts for a smart car that performed just as well as the production versions.Repair and remanufacturing
Aerospace manufacturers are expecting an increased demand for engines. “The number of aircraft engines needed is expected to be more than 114,000 by 2025, challenging aerospace engine manufacturers to reduce the environmental impact of manufacturing,” says Steve Beech, manufacturing process owner for joining at Rolls-Royce (Derby, England). “For some components, the buy-to-fly ratio can be as high as 13:1—meaning that for every 13 kilos of titanium bought, 1 kilo remains on the final component.”
The laser additive repair of seal segments for a high-pressure turbine aero engine is one example of an area where the environmental impact of new manufacture can be reduced. “The traditional manufacturing route for such a single-crystal component is to EDM the lattice that contains the abradable material into the solid base; it is this abradable lining that wears during service as the turbine blade seal fins rub into it,” says Beech (see Fig. 4). A conventional technique such as brazing a new lattice onto the seal segment was not feasible because the lattice walls were required to be less than 0.3 mm thick (and, with 34 segments in each turbine, very costly). “But by fusing a suitable powder using direct laser deposition to build up the lattice, the cost of repair was brought down to half the OEM cost,” says Beech.The laser cladding process has also been used at GE Aviation (Cincinnati, OH) for more than two decades. “Laser cladding is applied to the cost-effective refurbishment and hardfacing of both expensive and inexpensive field-returned hardware, such as high-pressure turbine and compressor blades for improved repeatability of process and automation,” says Sudhir Tewari, senior engineer, Laser Applications at GE Aviation. Tewari explains that laser cladding typically results in a low heat-affected zone and superior material properties—nearing that of the wrought material—due to fine dendritic microstructure obtained by the rapid solidification rate of the process. “GE participated in a Metals Affordability Initiative (MAI) for additive fabrication of nickel-based superalloy components and successfully demonstrated feasibility of laser additive deposition of such features,” says Tewari. “However, a lack of the availability of design-quality property data and the potential risk of internal defects in deposits remain some of the biggest challenges for application of such additive processes in manufacturing.”
Technological challenges
Phil Carroll, technical director at LPW Technology (Lymm, England), says that deposition rates vary between 20 g/hour for small AM components, up to 2 to 3 kg/hour for cladding applications, using laser power levels in the tens of watts to several kilowatts range. “But deposition rates are a deceiving target when you talk about laser AM; the real prize is metallurgical integrity,” says Carroll. He says that AM will benefit from the same process improvements as welding and cutting; for example, the well-controlled beam profiles of fiber and disk lasers enable fabrication of more-complex structures with very fine features and reduced residual stress, for potentially better and stronger microstructures. “Our group also looks at material issues such as powder grain sizes and shapes—parameters that contribute to a pore-free, crack-free structure in the essentially miles of weld that comprise an AM component.”
“Most of our time is spent educating customers about these technologies and proving they can be used for real manufacturing applications,” says Bruno LeRazer, DMLS manager at 3T RPD. “Even though the DMLS process has improved in the past few years due to ytterbium high-power fiber lasers that enable the use of potentially any kind of metal powders, there is still a lot of work to be done to bring many processes to a suitable production level.”
REFERENCES
- The Laser Institute of America’s (LIA; Orlando, FL) Laser Additive Manufacturing Workshop and the Association of Industrial Laser User’s (AILU; Abingdon, England) Additive Layer Manufacturing Workshop.
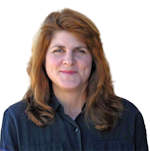
Gail Overton | Senior Editor (2004-2020)
Gail has more than 30 years of engineering, marketing, product management, and editorial experience in the photonics and optical communications industry. Before joining the staff at Laser Focus World in 2004, she held many product management and product marketing roles in the fiber-optics industry, most notably at Hughes (El Segundo, CA), GTE Labs (Waltham, MA), Corning (Corning, NY), Photon Kinetics (Beaverton, OR), and Newport Corporation (Irvine, CA). During her marketing career, Gail published articles in WDM Solutions and Sensors magazine and traveled internationally to conduct product and sales training. Gail received her BS degree in physics, with an emphasis in optics, from San Diego State University in San Diego, CA in May 1986.