LED FABRICATION: ILED array is a true flexible display
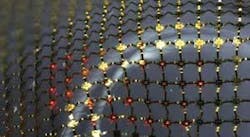
Flexible displays are not known for their durability. Often based on organic LED (OLED) technology, they suffer from a fundamental problem: if the display is to bend, the light-emitting pixels themselves must flex. (Nonemitting flexible displays, such as those based on E-Ink’s electrophoretic technology, also have the disadvantage of requiring flexible pixels.) This not only limits lifetime and choice of emitter material; it tends to restrict “flexing” to large-radius bends.
A new approach avoids this problem completely.1 Developed by scientists at the University of Illinois at Urbana Champaign (Urbana, IL), Semprius (Durham, NC), Northwestern University (Evanston, IL), and Tsinghua University (Beijing, China), the new display uses very small, very bright emitters. The high brightness of the emitters means they need only take up a tiny fraction of the pixel area—and can be rigid as a result. In addition, the approach makes transparent displays possible.
Inorganic LEDs (ILEDs), made of rigid semiconductor material, are the ideal emitter—bright, long-lasting, efficient, and spectrally pure. The researchers have devised a way to fabricate micro-ILEDs so that, after an etching process, they are removed from their semiconductor substrate when they contact a flexible mold. The mold can then be used to “print” the ILEDs (which can range from 25 to 250 µm square) onto the display substrate.
Novel printing process
The first prototype was based on red-emitting aluminum indium gallium phosphide (AlInGaP) ILEDs. Grown on an AlAs layer on a GaAs substrate, the 2.5-µm-thick ILEDs were laterally defined by plasma-reactive-ion-etched trenches; next, the AlAs was etched away, leaving each micro-ILED on two small photoresist posts. The mold—a soft elastomer stamp with relief features designed to contact selected ILEDs—was brought into contact and peeled away, with the ILEDs breaking off and sticking to the mold via the Van der Waals interaction.
The ILEDs can be printed onto many different types of materials, such as plastic, rubber, or glass. For example, a passive-matrix ILED array was fabricated on a rubber substrate using a noncoplanar conductor mesh, allowing the display to be stretched as well as bent (see figure).
Even the first prototypes show signs of true ruggedness. “We know that the ILEDs themselves are much more robust than OLEDs,” says John Rogers, one of the researchers. “When we integrate ILEDs on plastic or rubber substrates to make flexible or stretchable systems, respectively, we use theoretically optimized designs that minimize the mechanical strains that occur at or near the micro-ILEDs. Our paper shows fatigue cycling tests, of repeated bending and stretching, to roughly a thousand repetitions. For that level of fatigue, we see no change in properties. Of course, a commercial application would demand more rigorous testing, but based on what we see so far, things seem OK, consistent with theoretical modeling of the strain distributions.”
Path to commercialization
One of the establishments that contributed to the paper is Semprius, a start-up company launched two and a half years ago to commercialize printing systems and the devices they produce for use in the areas of electronics and photovoltaics. As a result, the manufacturing systems that would be used for the flexible ILED displays are reasonably well developed, although not quite yet configured for mass production, says Rogers. In addition, the delineation, undercut, and interconnection schemes for the displays can be carried out on commercial tools that are used in microelectronic and LCD manufacturing lines.
“A separate startup is in the process of pursuing applications in general lighting, and they are in the middle of negotiations for field-of-use sublicenses from Semprius for the printer, and from the University of Illinois for the ILED portion,” notes Rogers. (The same flexible-array technology has also been used by Rogers and other scientists to create a stretchable silicon-photodetector camera; see www.laserfocusworld.com/articles/336535)
Full-color ILED arrays are the next step. “We have already performed these processes successfully with gallium nitride (ILEDs that produce blue or green light),” Rogers says. “The details of the materials and processing are different, but the overall conceptual flow is exactly the same.” He notes that a manuscript on gallium-nitride-based devices is currently being prepared.
REFERENCES
- Sang-Il Park et al., Science 325, p. 977 (Aug. 21, 2009).
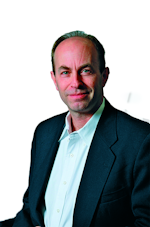
John Wallace | Senior Technical Editor (1998-2022)
John Wallace was with Laser Focus World for nearly 25 years, retiring in late June 2022. He obtained a bachelor's degree in mechanical engineering and physics at Rutgers University and a master's in optical engineering at the University of Rochester. Before becoming an editor, John worked as an engineer at RCA, Exxon, Eastman Kodak, and GCA Corporation.