LASER MICROMACHINING: Ultrafast pulses create superwicking grooves
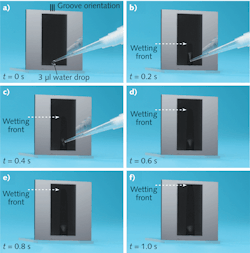
Everyone knows that cloth can wick water upward, but so can the surface of a crystalline material—if it is treated to give it the right structure. Anatoliy Vorobyev and Chunlei Guo at the University of Rochester's Institute of Optics (Rochester, NY) have done just this to silicon (Si), using femtosecond laser pulses to produce parallel microgrooves covered with even finer nanostructures.1 The resulting superwicking surface causes water to, in the words of the researchers, "sprint vertically uphill."
Laser scribing of grooves
Light from an amplified Ti:sapphire laser is focused to a 100 µm spot that is scanned over a 25 × 25 mm square of phosphorus-doped Si in air at atmospheric pressure to machine, one at a time, parallel microgrooves 40 µm deep and separated by 100 µm. The result is an extended array of grooves covering an area of 22 × 11 mm2. The surface is pitch black after machining—a result of the formation of nanoprotrusions and nanocavities, as well as larger microscale aggregates that result from the fusion of nanoparticles.
The researchers studied the surface's wicking properties both in the horizontal and vertical directions. Recording the process with a camera at 5 frames/s, they pipetted a 3 µl drop of water onto one end of horizontally placed grooves and measured the water speeding horizontally across the entire 22 mm distance in 0.6 s; the drop spread much more slowly in the vertical direction (3 mm in 4.2 s).
When the grooves were oriented vertically, the results were quite interesting. A similar-sized drop was placed at the bottom of the groove array; within 0.2 s, the wetting front had moved almost halfway up the 22 mm distance, and by 1.0 s, the wetting front had reached the top. In fact, the distance traveled by the wetting front as a function of time matched very closely with predictions from the Washburn equation, which calculates the motion of fluid as it wicks up a closed capillary tube, stating that the wicking distance depends on the square root of the time (see figure). The close match to the equation shows that, even with the added complex geometry of nano- and microstructures, the transport of water up the surface is due to the capillary effect.
The researchers tried similar experiments using other liquids, including methanol and acetone, and got similar results. In addition, knowing that the Si surface had oxidized during groove fabrication, and surmising that the chemical change could be affecting the water transport, they prepared a surface with the same geometry in a vacuum; the sample showed the same performance as the sample prepared in air.
Many potential uses
Vorobyev and Guo believe that the laser-structured superwicking surface could have application in nano- and microfluidics, chemical and biological sensors, lab-on-a-chip and other biomedical devices, and cooling and heat-transfer devices.
However, keep in mind that just as the ordinary wicking of water by a cloth does not violate any laws of energy conservation, neither does superwicking of water by Si; even if the water "sprints" upward, the energy needed to separate the elevated water from the Si surface so that the water could power a hypothetical waterwheel is greater than the energy the waterwheel would provide. So any ideas for perpetual-motion machines will have to be shelved for now.
REFERENCE
- A.Y. Vorobyev and C. Guo, Opt. Exp. 18, 7, p. 6455 (Mar. 29, 2010).
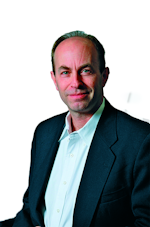
John Wallace | Senior Technical Editor (1998-2022)
John Wallace was with Laser Focus World for nearly 25 years, retiring in late June 2022. He obtained a bachelor's degree in mechanical engineering and physics at Rutgers University and a master's in optical engineering at the University of Rochester. Before becoming an editor, John worked as an engineer at RCA, Exxon, Eastman Kodak, and GCA Corporation.