PHOTOVOLTAICS: Laser processing yields solar cells with 22% efficiency
Solar cells made from crystalline silicon (Si) dominate the solar photovoltaic market. Typical conversion efficiencies of industrial crystalline Si solar cells are 14% to 16%, but novel laser-processing techniques can improve the photon-to-electron conversion process. Researchers at the Institut für Solarenergieforschung Hameln (ISFH; Emmerthal, Germany) have developed a solar-cell manufacturing sequence called rear-interdigitated single evaporation (RISE) for Si back-contacted solar cells based on laser processes that has pushed conversion efficiency up to 22%.1
Today, many companies use laser processing in the production of Si solar cells. BP Solar (Frederick, MD) uses a laser-grooved buried-grid technique in which a laser groove is machined into the Si surface and filled with metal to act as a front electrical-contact grid. The advantage of this process is reduced shadowing loss compared to standard front metallization. Advent Solar (Albuquerque, NM) uses a different method called emitter wrap-through in which highly doped walls of laser-drilled through-holes in the Si wafer conduct the current from the front side of the emitter to metal contacts placed on the back surface, further reducing shadowing losses.
Noncontact process
In the production process for the RISE solar cell, laser processing defines a patterned emitter and base region on the back side of the solar cell and laser ablation also allows reliable self-aligned contact separation after metallization (see figure). The noncontact process (important for reducing wafer breakage) first involves ablation of regions of a thin silicon nitride or silicon oxide layer placed over the back side of the crystalline Si wafer into an interdigitated pattern of emitter and base regions by a Q-switched, frequency-tripled (355 nm) Nd:YVO4 (vanadate) laser. Any crystal damage reduces the carrier lifetime and likewise reduces conversion efficiency. A potassium hydroxide (KOH) etching process removes this laser-induced damage. After etching, phosphorus diffusion creates the emitter region, leaving the raised silicon nitride and oxide areas as the base region. Next, a self-aligning contact-separation process of metal evaporation followed by wet chemical etching is used to separate the emitter and base regions.
To optimize the solar-cell conversion efficiency, the researchers of ISFH and of the Laser Zentrum Hannover (Hannover, Germany) explored carrier lifetime as a function of crystal damage by evaluating different laser sources and KOH etch depths.2 It was found that the depth of laser-induced damage for a frequency-tripled 355 nm laser was 3 µm, 4 µm for a frequency-doubled 532 nm laser, and more than 20 µm for a Nd:YAG 1064 nm laser.3 As long as the damage is removed to these depths, more than 20% conversion efficiency for the solar cell is not jeopardized; however, the etch depths need to be considered in terms of the required source-laser costs and the thickness of the Si wafers being used in the production process.
“The RISE concept uses laser processing as a key technology,” says solar-cell group head Rüdiger Meyer. “Since we use noncontact processes that are already known from other industrial applications in most cases, the production of the RISE solar cell is industrially feasible for thin, large-area crystalline Si wafers. This will result in costs that at least will be comparable to those of today’s standard solar-cell production.”
REFERENCES
1. P. Engelhart et al., Proc. 21st EUPVSEC 2006, Dresden, Germany, 773.
2. A. Schoonderbeek et al., paper M704, ICALEO 2006, Scottsdale, AZ.
3. P. Engelhart et al., paper M703, ICALEO 2006, Scottsdale, AZ.
About the Author
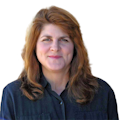
Gail Overton
Senior Editor (2004-2020)
Gail has more than 30 years of engineering, marketing, product management, and editorial experience in the photonics and optical communications industry. Before joining the staff at Laser Focus World in 2004, she held many product management and product marketing roles in the fiber-optics industry, most notably at Hughes (El Segundo, CA), GTE Labs (Waltham, MA), Corning (Corning, NY), Photon Kinetics (Beaverton, OR), and Newport Corporation (Irvine, CA). During her marketing career, Gail published articles in WDM Solutions and Sensors magazine and traveled internationally to conduct product and sales training. Gail received her BS degree in physics, with an emphasis in optics, from San Diego State University in San Diego, CA in May 1986.