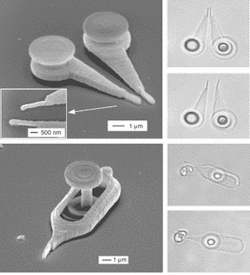
The tools contain fixed and moving parts and are fabricated using a two-photon stereolithographic process developed by the group. A focused spot produced by a pulsed 763-nm-emitting Ti:sapphire laser is scanned through UV-curable resin; as the structure forms, the movable portions are held in place only by the viscosity of the resin. The scanning pattern of the beam is optimized to compensate for distortion resulting from shrinkage of the resin. A rinse with glycol ether ester removes all uncured resin from the completed tool.
A set of tweezers was formed in six minutes, with the tools' fine points fabricated by point-by-point exposure (see figure). The same laser and optical system used to fabricate the tweezers was used to manipulate them, but the laser was operated in a continuous-wave rather than pulsed mode. One tweezers arm was fixed, while the focused beam moved the other arm. The gap was controlled very precisely—in contrast to electrostatically controlled microtweezers, which clamp shut suddenly as a certain actuating voltage is reached.
A slotted needle captured on a post was also constructed. A "dot" formed into one end of the needle is captured by the manipulating laser beam. The needle can be optically translated, rotated, or both. Using 200 mW of laser power, the needle was translated by up to 6.8 µm or spun to a rotational speed of 34 rpm. Speeds are proportional to laser power and are limited by viscous drag. A microscopic dust particle was manipulated by the needle; a prick by the needle did not deform the needle's tip.
The tools have biological uses, says Shoji Maruo, one of the Nagoya researchers. "These light-driven nanomanipulators will be widely applied to cell biology, single-molecule analysis, and other nanobiotechnology," he notes. "Our first application is manipulation and analysis of single molecules such as DNA and protein. The second is mechanical stimulation of a living cell. In the near future, these light-driven nanomachines will be integrated into microfluidic systems, so that automatic analysis of single molecules and cells may be possible."
REFERENCE
- S. Maruo et al., Appl. Phys. Lett. (Jan. 6, 2003).
Correction
We incorrectly credited the photo that appeared in Japanwatch, January 2003, p. 54. The Fig. 2 photo of an oscilloscope testing a 160-Gbit/s photonic network should have been credited to Ando Electric (Tokyo), not Sony Techtronics (which, in any case, should have been spelled Sony Tektronix). Laser Focus World regrets the error.
About the Author
John Wallace
Senior Technical Editor (1998-2022)
John Wallace was with Laser Focus World for nearly 25 years, retiring in late June 2022. He obtained a bachelor's degree in mechanical engineering and physics at Rutgers University and a master's in optical engineering at the University of Rochester. Before becoming an editor, John worked as an engineer at RCA, Exxon, Eastman Kodak, and GCA Corporation.