Carbon nanotube threads conduct electricity like metal
Houston, TX--Researchers at Rice University, Teijin Aramid (Arnhem, the Netherlands), the U.S. Air Force Research Laboratory (AFRL; Dayton, OH) and the Technion Institute (Haifa, Israel) have created carbon nanotube (CNT) wires that are as electrically conductive as metal, but act physically like textile thread.1 Such wires could be used in flexible displays, as well as flexible photonic sensors and arrays.
“We finally have a nanotube fiber with properties that don’t exist in any other material,” said lead researcher Matteo Pasquali, professor of chemical and biomolecular engineering and chemistry at Rice. “It looks like black cotton thread but behaves like both metal wires and strong carbon fibers.”
Sensors in clothing
“The new CNT fibers have a thermal conductivity approaching that of the best graphite fibers but with 10 times greater electrical conductivity,” says study co-author Marcin Otto, business development manager at Teijin Aramid. “Graphite fibers are also brittle, while the new CNT fibers are as flexible and tough as a textile thread. We expect this combination of properties will lead to new products with unique capabilities for the aerospace, automotive, medical, and smart-clothing markets.”
Shortly after arriving at Rice in 2000, Pasquali began studying CNT wet-spinning methods with the late Richard Smalley. In 2003, two years before his untimely death, Smalley worked with Pasquali and colleagues to create the first pure nanotube fibers. The work established an industrially relevant wet-spinning process for nanotubes that was analogous to the methods used to create high-performance aramid fibers—like Teijin’s Twaron—which are used in bulletproof vests and other products. But the process needed to be refined. The fibers weren’t very strong or conductive, due partly to gaps and misalignment of the millions of nanotubes inside them.
The next big breakthrough came in 2009, when Talmon, Pasquali and colleagues discovered the first true solvent for nanotubes—chlorosulfonic acid. “Until that time, no one thought that spinning out of chlorosulfonic acid was possible because it reacts with water,” says Pasquali. “A graduate student in my lab, Natnael Bahabtu, found simple ways to show that CNT fibers could be spun from chlorosulfonic acid solutions. That was critical for this new process.”
Pasquali said other labs had found that the strength and conductivity of spun fibers could also be improved if the starting material (clumps of raw nanotubes) contained long nanotubes with few atomic defects. In 2010, Pasquali and Talmon began experimenting with nanotubes from different suppliers and working with AFRL scientists to measure the precise electrical and thermal properties of the improved fibers.
In 2010, Teijin Aramid set up and funded a project with Rice, and the company’s fiber-spinning experts have collaborated with Rice scientists throughout the project.
“Metal wires will break in rollers and other production machinery if they are too thin,” says Pasquali. “In many cases, people use metal wires that are far more thick than required for the electrical needs, simply because it’s not feasible to produce a thinner wire. Data cables are a particularly good example of this.”
REFERENCE:
1. Science, 11 January 2013; DOI: 10.1126/science.1228061
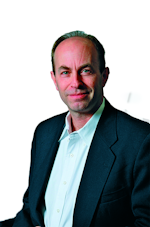
John Wallace | Senior Technical Editor (1998-2022)
John Wallace was with Laser Focus World for nearly 25 years, retiring in late June 2022. He obtained a bachelor's degree in mechanical engineering and physics at Rutgers University and a master's in optical engineering at the University of Rochester. Before becoming an editor, John worked as an engineer at RCA, Exxon, Eastman Kodak, and GCA Corporation.