International consortium to ramp up production of nanopatterned antireflective plastic films
Singapore--Scientists from A*STAR’s Institute of Materials Research and Engineering (IMRE) will partner with companies to develop, prototype, and conduct pilot large-scale manufacturing of nanoimprinted patterned plastic films having low reflectivity over large angles. The roll-to-roll process has a potentially lower cost than current production methods.
IMRE and its Industrial Consortium On Nanoimprint (ICON) partner companies are aiming to produce two types of patterned nanoimprinted plastic films. Potential applications of such mass-produced anti-reflective films are in the mobile device and tablet markets; the second type of film, a self-cleaning plastic, can be applied to surfaces such as building walls.
IMRE and five companies—Innox Higa Singapore Pte Ltd., Micro Resist Technology GmbH, NTT Advanced Technology, SABIC Innovative Plastics, and Solves Innovative Technology—will work together to develop the materials and scale up production of the films.
The partners are developing tougher resins for the nanostructures that will be patterned onto the plastics via IMRE’s nanopatterning process. The process will be scaled up using UV roll-to-roll nanoimprinters.
"We are a company that specializes in photoresists and polymers for micro and nanolithography," says Marko Vogler of Micro Resist Technology GmbH. "Within the ICON project, we will provide tailor-made polymer materials for nanostructured functional films. It is a unique opportunity for us to adapt materials specifically for roll-to-roll processes as well as for 'hard' industrial requirements which cannot be achieved by today’s off-the-shelf materials."
The pilot manufacturing project will last a year, after which the consortium will further develop and market the technology.
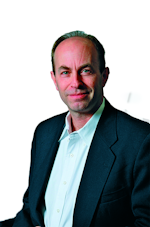
John Wallace | Senior Technical Editor (1998-2022)
John Wallace was with Laser Focus World for nearly 25 years, retiring in late June 2022. He obtained a bachelor's degree in mechanical engineering and physics at Rutgers University and a master's in optical engineering at the University of Rochester. Before becoming an editor, John worked as an engineer at RCA, Exxon, Eastman Kodak, and GCA Corporation.