Laser-activated resonator and nanostring creates chip-based optomechanical sensor
Lausanne, Switzerland--Scientists at École polytechnique fédérale de Lausanne (EPFL) have developed a rapid, precise optomechanical measurement system that can be embedded into a silicon chip. This new technology—that combines a disk resonator, a nanosized string, and a laser to sense tiny vibrations—could revolutionize the domain of sensors and atomic force microscopy.
As described in Nature Nanotechnology, when the tiny string comes into contact with a particle or a gas molecule, it vibrates. Each kind of molecule elicits a specific vibration, giving it a unique signature that can be used to identify the gas or suspended particle in the air, even in minuscule quantities. As resonators are miniaturized, the smaller the string, the more strongly it reacts when it comes in contact with a particle. With a string that's only a few hundred nanometers in diameter, the device developed at EPFL's Center for Micronanotechnology (CMi) is one of the most sensitive that can be operated at room temperature.
The scientists use a laser beam that’s directed into a tiny glass disk to analyze the string's vibrations. The beam circulates 1,000 times in barely 2 ns, and then exits the disk. The string is placed just above this photon track, and when it vibrates, it perturbs the beam. By comparing the wavelength of the laser when it enters the disk and when it leaves it, the scientists can deduce the movements of the string.
The main obstacle the team faced was a physical phenomenon known as Brownian motion that causes random vibrations on the string that amplify with every impact and take a certain amount of time to die off. This phenomenon significantly slows down measurements. This difficulty is typically overcome by cooling the system using helium, because Brownian motion is greatly reduced at ultra-cold temperatures. But the EPFL team was able to develop a technique that diminished the Brownian motion and still allowed the system to remain at room temperature. One laser, the "probe," detects movements in the string. The signal is processed in real time and used to modulate a second laser, the "control," which is injected into the disk to counteract the effects of the Brownian motion by exerting a counterforce on the string—a kind of virtual cooling system.
Using this innovative technique, the scientists were able to reduce the time between measurements 32-fold, while operating at about 20°C. This level of precision is extraordinary. "If instead of a string, we had a 100m-long bridge, we could, keeping all the same proportions, measure a deformation of a single nanometer, or one ten-thousandth of the diameter of a hair, in real time," explains Verlot, who was a co-author on the paper. The system developed at EPFL combines sensitivity—thanks to the size of the device—and rapidity (thanks to the control laser) all without a complex and expensive cooling system. Completely integrated into a silicon chip, the system lends itself to numerous possible applications, says Verlot. "Sensors are not the only area in which our system could prove useful. For example, it could also help improve atomic force microscopy systems—invented in the 1980s by Swiss physicist Christoph Gerber—and, at a more fundamental level, facilitate the observation and measurement of many phenomena."
SOURCE: EPFL; http://actu.epfl.ch/news/new-generation-sensor-combines-lasers-and-mechanic/
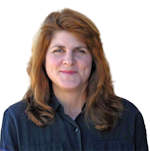
Gail Overton | Senior Editor (2004-2020)
Gail has more than 30 years of engineering, marketing, product management, and editorial experience in the photonics and optical communications industry. Before joining the staff at Laser Focus World in 2004, she held many product management and product marketing roles in the fiber-optics industry, most notably at Hughes (El Segundo, CA), GTE Labs (Waltham, MA), Corning (Corning, NY), Photon Kinetics (Beaverton, OR), and Newport Corporation (Irvine, CA). During her marketing career, Gail published articles in WDM Solutions and Sensors magazine and traveled internationally to conduct product and sales training. Gail received her BS degree in physics, with an emphasis in optics, from San Diego State University in San Diego, CA in May 1986.