Solar pumping converts broadband sunlight into efficient laser light
A team of researchers led by Dawei Liang, an associate professor at NOVA University of Lisbon in Portugal, are eschewing semiconductor laser arrays and embracing the promise of direct solar pumping of solid-state lasers to overcome current performance limitations and enable reliable operation of spaceborne lasers for years.
Broadband sunlight can be converted into laser light by solar pumping, which can be a source of narrowband, collimated, rapidly pulsed radiation—with the possibility of extremely high brightness and intensity.
“Since solar energy is the most abundantly available and reliable power source in space, 10x more than on Earth, space-based laser power generation would be a major step forward in terms of fulfilling energy needs,” says Liang. “The strength of sunlight in space is nearly twice that of on Earth, and there are 4 or 5x as many hours of sunlight, thanks to the absence of clouds and especially Earth’s night hours.”
Two significant shortcomings of semiconductor laser arrays are performance degradation over time and a limited lifespan—and seem to scale with the level of average output power.
Replacing semiconductor laser arrays with direct solar-pumped solid-state lasers “shows potential to overcome these limitations,” says Liang. “Terrestrial applications may become more obvious if an efficient and cost-effective renewable laser can be operational for laser material processing.”
How do you design a three-Ce:Nd:YAG rod solar laser system?
The team’s solar energy collection and concentration approach (see Fig. 1) uses a NOVA heliostat-parabolic mirror system composed of a large plane mirror with two flat segments mounted onto a two-axis heliostat—a device that turns to keep sunlight reflected toward a stationary parabolic mirror installed within a solar laser laboratory.
Their heliostat mirror has 93.5% reflectivity and redirects incoming solar radiation toward the stationary parabolic mirror with a 1.5 m diameter, 60° rim angle, and 660 mm focal length. The parabolic mirror’s back surface is coated with silver, and its reflectivity is 80% for this primary mirror.
“Our solar laser head component is made of a large fused silica aspheric lens and three 2.5-mm-diameter, 25-mm-length Ce:Nd:YAG rods mounted within the single conical pump cavity (see Fig. 2, left),” says Liang. “And we aligned three small partial reflection 1064-nm output mirrors with corresponding laser rods (see Fig. 2, right).”The team was able to get accurate resonant cavity alignments by adjusting three output couplers individually by their respective positioners. “For accurate alignment within the focal zone, we mounted the laser head onto the X-Y-Z axes positioning systems,” says Liang.
Their fused-silica aspheric lens has 84 mm diameter, 37 mm thickness, 44 mm front-surface radius of curvature, and -0.005 rear aspheric coefficient r2 parameter.
“Our aspheric lens efficiently coupled the concentrated solar radiation from the focal zone into the three Ce:Nd:YAG rods within the single conical pump cavity,” Liang notes. “For end-pumping, we directly focus one part of the concentrated radiation onto the Ce:Nd:YAG rod through the high-reflection (1064-nm) end face of the rods by the aspheric lens. The coatings reflect the 1064 nm oscillating laser beam within the resonant cavity, while permitting the entrance of other useful solar rays for pumping.”
For side pumping, another part of the solar rays not passed through the high-reflection 1064 nm end face of the Ce:Nd:YAG rod get coupled into the conical pump cavity. “A zigzag passage of the solar arrays within the pump cavity ensures efficient multi-pass side pumping to the rods,” says Liang. “And we glue the inner wall of the pumping cavity with a protective silver-coated aluminum foil of 94% reflectivity.
Putting the solar laser to the test
Liang and colleagues put their single-laser/three-beam Ce:Nd:YAG rod solar laser pumping method to the test (see Fig. 3) and it provides efficient simultaneous emissions of three continuous-wave 1064 nm beams—with a 4.64% solar-power-to-laser-power conversion efficiency, a 41.25 W/m2 solar laser collection efficiency, and a calculated 7.64% solar laser slope efficiency.“Our method achieves high compactness because one laser produces several laser spots—each precisely controllable with a minimum heat input on each of the three thin Ce:Nd:YAG laser rods within a single pump cavity,” explains Liang. “This provides a much more stable laser outputs and the ability to tailor the applied energy to the specific needs for laser materials processing applications.
The team’s solar laser may find wide-ranging applications such as earth, ocean, and atmospheric sensing, laser beaming, deep space communications, and space debris removal.
Liang and colleagues are now attempting to pump four and seven thin Ce:Nd:YAG rods within the conical pump cavity to enhance the solar-to-laser conversion efficiency to more than 5% and achieve total laser output power stability of less than 0.5% within the solar tracking error range of ±0.2°.
FURTHER READING
D. Liang et al., Sol. Energy Mater. Sol. Cells, 246 (2022); https://doi.org/10.1016/j.solmat.2022.111921.
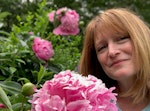
Sally Cole Johnson | Editor in Chief
Sally Cole Johnson, Laser Focus World’s editor in chief, is a science and technology journalist who specializes in physics and semiconductors.