Industry-grade terahertz time-domain spectroscopy system has kilohertz measurement rates
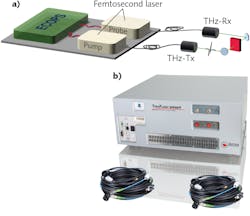
Inline thickness gauging is currently among the most promising industrial applications for terahertz optical technologies. Acting on this demand, TOPTICA Photonics (Gräfelfing, Germany) has developed a terahertz time-domain system based on electronically controlled optical sampling (ECOPS), which is designed to measure terahertz pulses at kilohertz rates to permit inline measurements even in harsh industrial environments.
Nondestructive thickness measurements using terahertz time-domain spectroscopy (TDS) systems play an increasingly important role in industrial quality control, cost management, and process monitoring. Promising applications include, for example, inline control of polymer parts during extrusion and analysis of paint and coating layers in multilayer stacks.1
Although the foundations for the technology were laid back in the 1990s, the usability of terahertz systems remained restricted to research labs for many years. The main reason was simply a lack of industrial maturity, with examples including prohibitively high costs, large instrument sizes, poor robustness, limited signal quality, and insufficient measurement speed from some platforms. In addition, inexpensive established alternatives existed that dominated the market for nondestructive testing, such as ultrasonic sensors and x-ray devices. Industrial quality-control applications have high requirements for their measurement systems—for example, they have to withstand harsh environmental conditions such as temperatures ranging from 15° to 45°C along with strong vibrations, while still allowing for thickness measurements with micrometer or even submicrometer resolution at high scan rates in the kilohertz range.
Terahertz TDS systems have improved and matured over the last two decades, leading to several technological approaches currently available on the market. Typical commercialized systems use femtosecond fiber lasers and photoconductive switches for terahertz generation and detection. The pump-probe technique used for time-resolved detection of terahertz pulses requires a variable time delay in order to sample the terahertz waveform with a time-shifted copy of the laser pulse. The quality of the delay turns out to be a crucial factor for the system performance. Conventional TDS spectrometers mostly use mechanical delay lines; while enabling highly precise measurements, the required mechanical movement limits the acquisition rates (the number of waveforms per second) usually to values between a few hertz to about 100 Hz at most. Some particular mechanical scanners are able to achieve kilohertz rates, but with limited delay length and with the sacrifice of flexibility. Moreover, mechanical delays comprise high-precision optical elements, which not only drive the costs for these assemblies but also make them susceptible to vibrations and misalignment.
Industry-grade terahertz TDS systems
To meet the above-mentioned industrial requirements, a terahertz TDS system based on ECOPS has been developed, which pushes signal acquisition rates into the kilohertz range.2 Such TDS systems use two synchronized femtosecond lasers (see Fig. 1a). The repetition rate of one laser is modulated to achieve a variable time delay between the two lasers, which eliminates the expensive mechanical delay with its alignment-sensitive free beam components and moving parts altogether.With ECOPS, even measurement rates up to 10,000 waveforms per second have been demonstrated.3 Moreover, ECOPS-based systems benefit significantly from operating at telecom wavelengths. This involves the use of 1550-nm fiber lasers with reliable 24/7 pushbutton operation, as well as progress made with fiber-coupled indium gallium arsenide (InGaAs)-based terahertz antennas offering higher output power. The replacement of free-space optics with fiber optics and, as mentioned before, the substitution of mechanically moving parts by phase-locked loop electronics (ECOPS), enables fast and reliable measurements even under harsh conditions. Thus, these systems now have a compact footprint (see Fig. 1b) ready for integration in a 19-in. rack; in addition, one can take full advantage of both the low prices and the high reliability of standardized telecom components. A long fiber delivery between the main unit and the sensor head enables flexible integration into industrial quality-control setups. Moreover, the system complies with industry test standards as well as radio and laser safety regulations.
In a demonstration of the system’s performance, Figure 2a depicts the time-domain trace of a single-shot measurement acquired with an ECOPS system within 625 µs (green curve), together with an average of 1000 pulse traces (black). While the main pulses appear virtually indistinguishable, the averaged trace exhibits a significantly reduced noise floor, which is particularly evident in the pre-pulse background signal (inset). The time-domain dynamic range of the system for the single-shot measurement is better than 50 dB—a record value at kilohertz measurement rates.
Another relevant parameter for terahertz TDS systems is the spectral bandwidth. Figure 2b shows terahertz power spectra, calculated by a fast Fourier transform of time traces obtained with the TOPTICA ECOPS setup at 1600 Hz. In a single-shot measurement, the system achieves a peak dynamic range (PDR) of 38 dB and the signal reaches the noise floor at 3.4 THz. All of the dips observed in the spectrum correspond to literature values of water-vapor absorption lines, as documented in the HITRAN database.4 With 1000 averages, the PDR increases to 68 dB and the detectable signal extends to approximately 4.8 THz, still within a measurement time of only 0.6 s.
Depending on the requirements of the specific application, the measurement rate can be flexibly selected between 200 and 1600 terahertz pulse traces per second, resulting in scan ranges between 700 ps and 150 ps, respectively. The long scan range (700 ps) enables thickness gauging up to about 7 cm (in reflection, assuming a double pass through a sample with a refractive index of 1.5). This flexibility, combined with an excellent DR and SNR values, makes the ECOPS system very suitable for thickness gauging applications.
Inline thickness gauging
Terahertz TDS systems are deployed in several industrial applications, including quality control of coatings.1 Thickness gauging is based on contactless reflection measurements, enabling easy integration into production lines with one-sided access. The fundamental principle for the thickness evaluation is a time-of-flight analysis of the terahertz pulses partially reflected from each interface in the sample, akin to the ultrasound approach. Sophisticated data-analysis techniques such as deconvolution and mathematical modelling of transfer functions make it possible to analyze multilayer coatings on any substrate and distinguish each individual layer. Commercial systems can measure coating thicknesses down to 5–10 μm with an accuracy better than 1 μm and a reproducibility below 1%.1 Yet, to perform these measurements inline at kilohertz rates, faster scanning techniques are required.
Here, suitability of the fast ECOPS-based system is demonstrated for direct inline thickness gauging in a production line. A vinyl-record player is used to mimic a sample speed similar to that of an actual conveyor belt or extrusion line. The sample consists of an aluminum plate with a manually applied paint layer (see Fig. 3 inset). The record player rotates the sample (circumference of about 0.86 m) at 45 rotations per minute, equal to a lateral velocity of about 1.15 m/s at the edge of the plate. Owing to the high measurement rate of the ECOPS system, the sample thickness can be evaluated with a spatial resolution of approximately 0.7 mm (not considering the actual focus size). For data analysis, a fast algorithm is used to calculate thickness information directly from time-of-flight measurements of the reflected terahertz pulses, enabling real-time analysis of the data.As seen in the Figure 3 graph, the thickness measurement starts at position 0 and ends at position 660. The thickness of the paint layer is resolved with micrometer precision and values varying between about 130 µm and 550 µm. The red layer is thinner than the blue layer and the transition between two layers at position 507 appears as an abrupt increase in the thickness. With these measurements, the excellent performance of the system is demonstrated. As of today, this combination of a high-speed ECOPS-based system with reliable inline data analysis provides the fastest thickness measurements for a commercial terahertz TDS system.5
Terahertz time-domain systems have arrived in the nondestructive-testing market; among the most promising quality control applications are thickness gauging of paints and coatings, as well as the inline control of plastic components during extrusion. Further industrial and scientific applications for fast terahertz systems include imaging, defect detection, and spectroscopy, especially when investigating fast-moving samples or measuring under varying environmental conditions.
Key to terahertz-systems market success is a flexible, cost-efficient, robust, and compact design fully based on telecom components and a fast scanning technique called ECOPS. The system complies with industry test standards and is ready to be operated, even in a harsh environment. The demonstrated high signal quality at record measurement rates in the kilohertz range enables reliable inline thickness measurements with micrometer precision.
The trends for terahertz applications require faster scanning techniques and more-precise measuring systems to image samples with larger areas or to detect micrometer-thin layers. Active research areas include improved emitters and detectors, as well as optical sampling techniques such as single-laser polarization-controlled optical sampling (SLAPCOPS),6 resonant electronically controlled optical sampling (RECOPS),7 and timed asynchronous optical sampling (TASOPS).8
REFERENCES
1. M. Naftaly et al., Sensors, 19, 4203 (2019).
2. R. J. B. Dietz et al., Opt. Lett., 39, 6482–6485 (2014).
3. M. Yahyapour et al., “Non-contact thickness measurements with terahertz pulses,” Proc. 19th World Conference on Non-Destructive Testing (2016).
4. L. S. Rothman et al., J. Quant. Spectrosc. Radiat. Transf., 130, 4–50 (2013).
5. M. Yahyapour et al., Appl. Sci., 9, 1283, (2019).
6. M. Kolano et al., Opt. Lett., 43, 1351–1354 (2018).
7. German Patent DE102015113355B4.
8. U.S. Patent US9685754B2.