PHOTONICS APPLIED: MACHINE VISION: Single-stream recycling challenges machine-vision capabilities
“Paper or plastic?” Truly a question pondered by most everyone in the developed world. The desire for a sustainable economy and “green” management of our environmental resources has driven the ordinary consumer to be more aware of our individual consumption habits. Fortunately, most developed nations with active recycling programs are making the process easier for the average consumer. But even though single-stream recycling means we can put paper, plastic, metal, and other recyclables in the same container, the real responsibility falls on the backs of the machine-vision systems used to sort these items.
Optical sorting systems from such American and European companies as General Kinematics (Crystal Lake, IL), Lubo (Emmen, the Netherlands), McCloskey International (Peterborough, ON, Canada), Mogensen (Grantham, England), MSS (Nashville, TN), Pellenc (Pertuis, France), S&S Separation (Schönberg, Germany), Sherbrooke O.E.M. (Quebec, QC, Canada), and TiTech (Stamford, CT) are direct benefactors of machine-vision advances in camera speed, resolution, and in ongoing development of unique vision algorithms. So just how successful are these machine-vision systems? Is manual sorting still necessary for some applications?
When vision steps in
In most single-stream recycling applications, rotating devices can separate lighter materials like cardboard and paper from heavier objects like bottles and metals that fall to another level. Magnets can remove steel and tin cans from the mix, leaving primarily glass, plastic, and nonmagnetic metallic items. It is here where machine vision steps into the picture.
In late 2009, Waste Management of Orange County installed a $1.7 million dollar recycling sort line with TiTech infrared optical sorting capability that will increase waste diversion (recover recyclable material) by 30,000 tons per year, with a processing rate of 15 tons per hour.1 The TiTech system is representative of how most optical sorting systems work: A light source, typically infrared (IR) or near-infrared (NIR), illuminates materials moving on a conveyor belt. Multiple sensors analyze the spectral signal of the reflected light, which is unique for different materials. The spectral (or multispectral or hyperspectral) signal is converted to a visual image using colors or patterns and the object’s visual image is used to identify the physical location and makeup of the object. Typically, hundreds of separate jets of air from a nozzle then push different items into separate bins.
Eagle Vizion (Sherbrooke, QC, Canada), who works closely with system provider Sherbrooke, develops optical sorting systems that use NIR spectroscopy over a full range from 1100–2500 nm. Different wavelength ranges are used to distinguish different waste streams at analysis speeds up to 200 Hz. Eagle Vizion says that NIR spectroscopy is still not adequate for very dark to black materials, and that manual sorting is still required for these and some other materials—especially for plastics and glass contaminated with foils and residues. But despite these drawbacks, “Most companies have optical sorting efficiencies around 80%, with some as high as 95%,” says Nathanaël Lortie, president of Eagle Vizion. “This efficiency increases by making sure that waste components are visually separated in a high-speed, in-line process.”
But in addition to spectroscopy, many other "vision"-based techniques such as visual color sorting and even x-ray fluorescence are used for optical material analysis. Unfortunately, if you ask any of the major machine-vision equipment providers, they will tell you that their optical techniques are "proprietary." Indeed, it was difficult to gather specific information on how these optical sorting technologies work. Fortunately, some companies were more forthcoming than others.
Plastic and paper sorting
Xenics (Leuven, Belgium) supplies IR and NIR sensors and camera systems for a variety of recycling applications. For plastics sorting, their IR sensors operate over the range from 1000–2500 nm; however, this range is not always adequate to cover all customer needs.
For plastic sorting, preshredded 3–5 cm plastic pieces enter a separation chamber where the reflected illumination is sent to a two-dimensional (2D) transmission spectrometer that produces a spectrum at each point of a single scan line across the conveyor belt. A 900–1700 nm indium gallium arsenide (InGaAs) sensor then reads the 2D transmission information and converts it to a spectral signature that is compared against a stored database to identify the material passing by for sorting. But unlike other InGaAs detectors with sensor array and readout circuits arranged with multipole, hybrid, wirebond, and 3D interconnect schemes, Xenics uses a multipole flip-chip technique wherein the sensor and readout circuit are placed directly on top of each other, permitting very compact sensor designs and machine-vision cameras as small as 5 × 5 × 5 cm3.
For those difficult black plastic parts, Xenics adds color analysis to IR spectral analysis using a combined visible and IR sensor with sensitivity from 400–1700 nm. Because the InGaAs sensor can be damaged by strong absorption of visible and NIR (up to 900 nm) wavelengths, Xenics thins the sensor chip to 5 µm by removing nearly 120 µm of the indium phosphide (InP) substrate, rendering it essentially transparent to visible light and enabling operation over the full 400–1700 nm range.
Reflective, transmissive, or transflective sensor setups in the ultraviolet to mid-infrared wavelength range are used by MSS depending on the application and materials that are targeted for identification and separation. For example, different types of plastic resins are identified using reflective near-IR absorption spectroscopy in the 1100–1750 nm range. Most of these sensor technologies use halogen light as the (broadband) illumination source. For certain specific applications, sensor systems out to 2500 nm are used. For the separation of flame-retardant plastics in electronic scrap, MSS uses dual-energy x-ray technology. And MSS builds the fastest paper grade sensor in the world—materials are transported through a 2.4 m wide sensor area at speeds of 6 m/s. A MultiWave sensor uses pulsed narrow-bandwidth color and near-IR LEDs as the illumination source. Using similar LED technology, the MultiWave also includes a sensor to measure glossiness and a fluorescent-based sensor to measure lignin/wood content in paper.
Glass sorting
For glass sorting, removal of metals, minerals, organics, leaded glass, and glass ceramics (heat-resistant glass) is necessary even before green, clear, and brown glass can be extracted and separated. For the approximate 11.5 million tons of waste glass from Europe alone in 2008, BT-Wolfgang Binder GmbH (Gleisdorf, Austria) uses x-ray fluorescence in its Redwave-branded optical sorting systems to specifically remove leaded glass and glass ceramics from the typically 10-60 mm sized, precrushed glass particle stream. Their sorters typically achieve separation efficiencies for glass ceramics and leaded glass of >95%.
Construction-material sorting
Waste from the construction industry typically consists of wood, brickwork, concrete, gypsum, roof material, paper, plastic, and a variety of metals. Under the “KRINGBOUW” industrial project, Delft University of Technology (TU Delft, the Netherlands) and several industrial collaborators studied various mechanical and optical methods for construction-waste separation.2 The project found that for color sorting, a Scan & Sort CombiSense 1200 from Separation Systems Engineering (SSE; Wedel, Germany) used at the Department of Mineral Processing at RWTH Aachen University (Aachen, Germany) could sort construction materials at a rate of 10 tons per hour. The CombiSense incorporates a high-speed camera that can recognize 1 billion colors and includes a special conductivity sensor that can identify a variety of metals. With wood, red brick, gypsum, and glass recovery values of 83%, 17%, 94%, and 96%, respectively, color sorting varies in efficacy for a variety of construction materials.
The KRINGBOUW project also looked at x-ray sorting with a Mogensen MikroSort AR 1200 and found that an effective split between organic and inorganic products could initially be made, followed by a more rigorous analysis using dual-energy x-ray transmission that could, for example, remove PVC from mixed combustible materials.
A growth industry
To put the recycling market in perspective, one of the companies I spoke with was planning to attend the “largest plastics recycling show in North America.” Held Mar. 2–3, 2010 in Austin, TX, the Plastics Recycling Conference boasted more than 700 attendees last year and around 90 exhibiting companies. Compared to the 18,000 attendees and 1100 exhibitors at Photonics West 2010, the Plastics Recycling Conference numbers give some indication that recycling is still an emerging market.
According to the US Environmental Protection Agency (EPA), Americans generated 250 million tons of municipal solid waste in 2008 and recycled 33.2% of it. Finding the statistic a bit surprising, I dug a little deeper and learned that the EPA does not keep statistics on total waste generation in the U.S.; however, information at www.zerowasteamerica.org says that municipal waste only accounts for as little as 2% up to 20% of all waste generated, with recycling statistics unknown. Even if municipal waste is as much as 20% of all waste in the United States alone, that brings the total of US waste to 1.25 billion tons. Clearly, waste recycling is a growth industry in the US and worldwide, considering that many developing countries have few recycling programs in operation.
REFERENCES
1. www.recyclingtoday.com/waste-management_orange-county_mrf.aspx
2. www.kringbouw.nl/kringbouw/data/publiek/nieuws/bestand_CDWRecSortierKollBerlin05.pdf
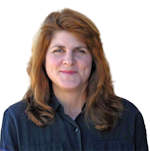
Gail Overton | Senior Editor (2004-2020)
Gail has more than 30 years of engineering, marketing, product management, and editorial experience in the photonics and optical communications industry. Before joining the staff at Laser Focus World in 2004, she held many product management and product marketing roles in the fiber-optics industry, most notably at Hughes (El Segundo, CA), GTE Labs (Waltham, MA), Corning (Corning, NY), Photon Kinetics (Beaverton, OR), and Newport Corporation (Irvine, CA). During her marketing career, Gail published articles in WDM Solutions and Sensors magazine and traveled internationally to conduct product and sales training. Gail received her BS degree in physics, with an emphasis in optics, from San Diego State University in San Diego, CA in May 1986.